A Powerful Upgrade
Linda Laframbois | Waupaca FoundryPositioning Waupaca Foundry’s Plant 4 for the Future
As a company built on hard work, innovation, and valuing its employees, Waupaca Foundry stands strong as the most respected iron foundry company in the world. But in an industry where technology is ever evolving and the lifespan of electrical equipment is relatively short, keeping up with capital improvements and automation is vital to improving cost structure, work safety, and iron casting quality and delivery.
True to the foundry’s culture of continuous improvement and world-class operating practices, in 2017, Waupaca Foundry began to evaluate operations and complete critical equipment and electrical-system upgrades at its Marinette ductile iron foundry. The power-service upgrade, slated for completion in 2023, will improve equipment operation and employee safety, offset inflation, and lay the foundation for accommodating future business growth and customer needs.
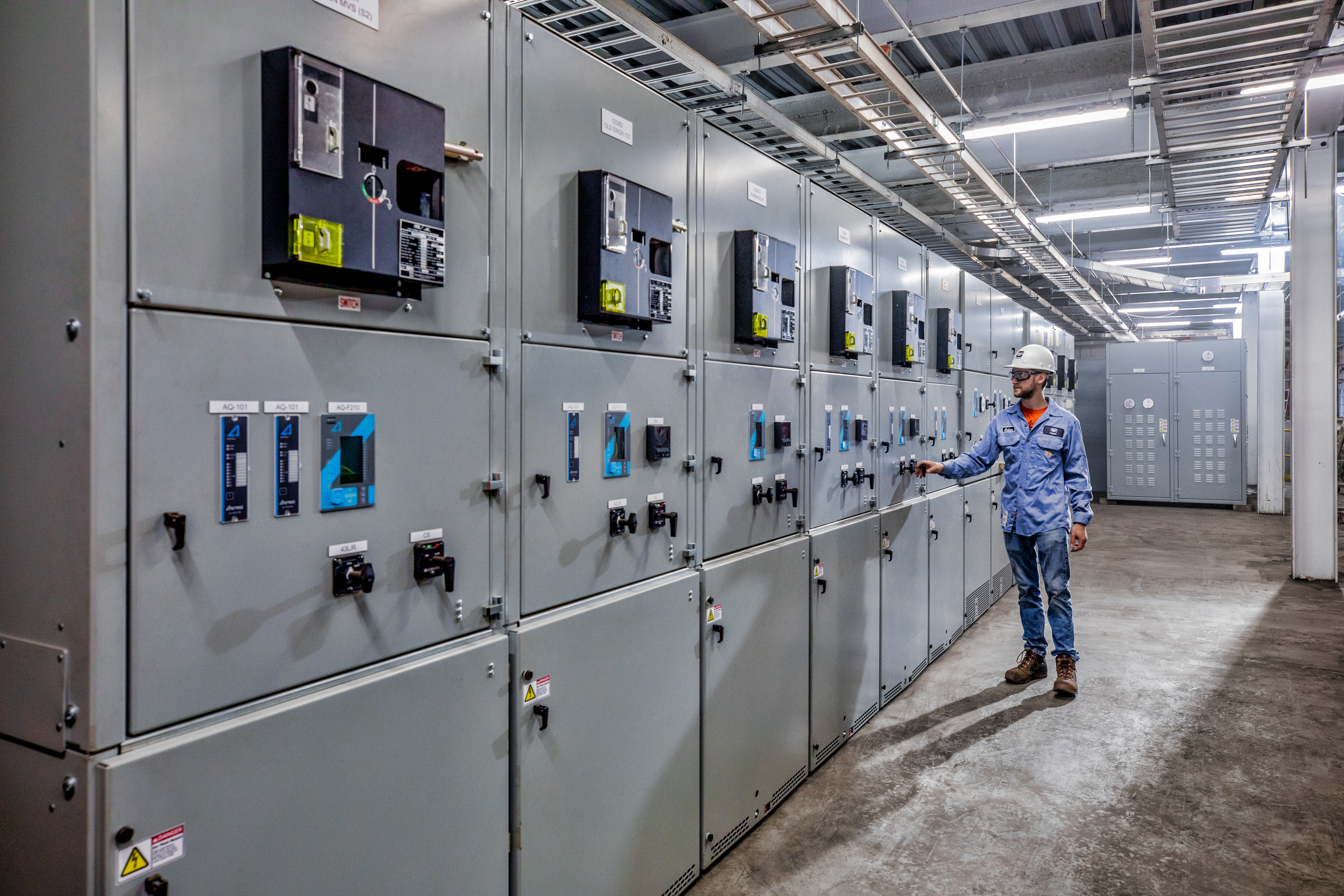.jpg?width=300&height=199)
Pictured above is Andrew Stalheim | Mechanical Projects Engineer
The power-service project involves upgrading feeders for medium-voltage power coming from the substation to the plant, securing new equipment for receiving the power, and installing state-of-the-art systems that distribute that power across the plant and to the melt center—where raw and scrap materials are melted to create new iron castings.
“This is an exciting multi-year effort involving Wisconsin Public Service, foundry engineers, and energy consultants,” said Marco Gonzalez, corporate energy manager at Waupaca Foundry. “Our objective is to upgrade the plant’s electrical system and incorporate smart technology and top-of-the-line power distribution -equipment to create a safe environment for our employees and a reliable system that supports us delivering the products our customers depend on.”
Safety First
Waupaca Foundry Plant 4, located in Marinette, Wis., is the largest single-user facility in Wisconsin Public Service’s (WPS) footprint. The ten 40-ton induction furnaces that melt iron to make parts for light vehicles, agricultural equipment, trucks, and trailers use 75 percent of the medium-voltage electricity that feeds into the facility.
Prior to the electrical system upgrade, power entering the plant fed into switches made in 1974 or 1992. The old switches contained very large fuses, much like a fuse in a house, only bigger. When there was an overcurrent or short, the fuse would blow, causing an industrial-sized arc.
To increase the safety of the systems and provide a safer work environment, old fuse switches will be replaced with new, state-of-the-art circuit breakers installed in dead-front switchgear with arc-flash protection capabilities, providing an extra layer of safety for our employees and the equipment nearby. Should an overcurrent or power surge occur with the new hardware, the circuit breaker will open, greatly reducing the likelihood of an electric explosion
A Better Work Environment
With new circuit breakers in place, the Marinette ductile iron foundry will move from a National Fire Safety Protection Association’s personal protective equipment (PPE) rating of PPE Category 4 (requiring an arc-rated flash suit, hood, and rubber gloves) to Category 0. That means employees could wear comfortable PPE in the melt and molding departments, such as untreated cotton long-sleeve shirts and pants, hard hats, ear plugs, safety glasses, and gloves.
In addition, all the new equipment is in a new climate-controlled building, improving the work environment for the people operating and maintaining the power system.
Meeting Compliance Standards
According to Robert Jezwinski, Jr., engineering manager at Waupaca Foundry, another project objective was to gain compliance with the National Electric Code. The ductile iron foundry’s original system was built in 1992, and some of the compliance standards have changed over the years.
“We worked with Wisconsin Public Service to understand what areas of the system were no longer in compliance,” said Jezwinski. “Our goal was to come up with a design that brought the plant and equipment back into compliance with the National Electric Code.”
Reliable and Responsive
An electric melt furnace failure caused by an arc flash translates to upwards of $200,000 in repair costs and approximately one month of equipment downtime due to the complexity of repairs and difficulty of procuring replacement parts. Upgrading circuit breakers translates into significant cost savings and operational reliability for the plant.
Moreover, smart devices are being added to the new system to allow operation, maintenance, and engineering teams to make better decisions in response to a fault and use real-time data to act in a predictive way before the fault happens.
Responsible Use of Resources
Waupaca Foundry’s power-service project will upgrade a normal delivery of power to a highly dependable, highly secure system that considerably improves the Marinette plant’s operations, work environment, and production reliability. “Having a reliable, updated, world-class electrical system was mandatory and the right thing to do for the plant,” said Gonzalez.
“As we look ahead to the next 30 or 40 years, we can count on having more technology and more automation. This new system has spare capacity that the previous system didn't have to address those future needs,” added Jezwinski. “As we continue to adopt new automation on the production floor in years to come, we will be equipped to provide safe and reliable electrical power energy to supply those operations and meet the evolving needs of our customers.”
We use cookies and other tracking technologies to personalize content and analyze our site traffic. More information about this is in our Privacy Policy. You can control third party cookies by adjusting your browser settings.