Best Casting Conversion Award
Mackenzie Morey | Waupaca FoundryThrough open communication, development, and realization of the quality of ductile iron, Waupaca Foundry
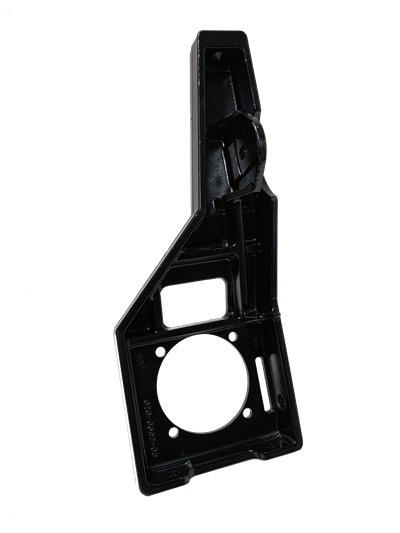
American Foundry Society Awarded Waupaca Foundry "Best Casting Conversion."
eliminated Bad Boy Mowers’ current strength issues and exceeded their quality expectations. While a change in the makeup of a part may be intimidating, the product design to just one single part emphasizes iron castings and the production complexities it can eliminate.
Bad Boy Mowers was looking to improve the quality and durability of the eight-piece steel weldment, rear suspension trailing arm on their Commercial Zero-Turn Mower, fabricated internally. However, the fabricated weldment’s strength did not withstand impact testing, and with the many components of the weldment, the fit was never perfect, resulting in gaps. The company realized that converting the weldment to a casting improved the overall quality, reduced warranty costs, and improved assembly.
Tooling engineering at Waupaca Foundry led the design of the casting. As a proactive measure, assembly models were used to compare the 8-piece weldment to the single ductile iron casting prior to production. Bad Boy Mowers recognized the improvements the casting would have on its operations and approved tooling to start on the project. The rear suspension features a cast 3-link trailing arm—the first and only of its kind in the industry. Matched with front suspension arms, the result is a smoother ride, more consistent tire contact, and increased hillside stability for the consumer.
Waupaca Foundry was awarded the “Best Casting Conversion” for a rear suspension trailing arm.

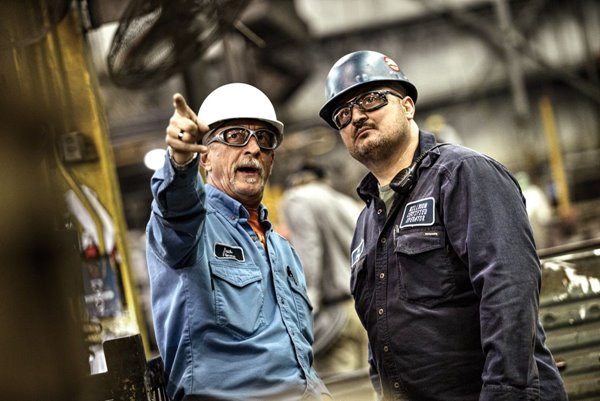