From 2014 to 2016, Waupaca Foundry increased casting core quality, production efficiency, and worker safety and comfort at both gray iron foundry plants located in Waupaca, Wis. Improvements allow for future expansion to meet future customer demand.
Building for the Future
Brian Sandalow | Modern Casting | AFSBuilding for the Future
Fortunately for the industry, many metalcasters are making additions or building brand new structures to help their companies grow and better serve customers. Modern Casting reached out to see how these firms are doing in their construction projects, what challenges they’ve overcome, and what kind of advice they’d give other companies planning to undertake important and possibly transformative projects.
Waupaca Foundry (Waupaca, Wisconsin)
AFS Corporate Member Waupaca Foundry (Waupaca, Wisconsin), a Hitachi Metals company, expanded core production at two of its Waupaca-based gray iron foundries, and the project is now complete. One robotic cell is running at Plant 1 and six robotic cells are running at Plant 2/3.
Getting there, however, was a process.
At Plant 1, the first phase saw 11,500 sq. ft. of storage space added for storage of sand cores, and the second phase was the construction of a 25,000 sq. ft. core production facility. Meanwhile, at Plant 2/3, the first phase included the addition of a core production facility with three double-wide warm-box coremaking cells. The plant also developed new robotic work cells, a sand conditioning system, a new way to distribute material, a new additive system and a new core-drying oven. In the next phase at Plant 2/3, one new and two double-wide warm-box coremaking cells were moved to the facility. A pair of robotic cells were moved and a robotic cell was added.
In doing this, Waupaca took a legacy foundry process and redesigned it from the ground up. Waupaca reviewed its production process and improved it via Kaizen best practices before designing the space. That allowed it to automate features to achieve repeatable quality results, improve ergonomics for worker comfort, and leave room to expand to meet future customer requirements. At Plant 2/3, Waupaca completed two phases of design, engineering, construction and implementation within a condensed 26-month timeline while decommissioning existing equipment in order to commission the new cells. This was all done while maintaining production capacity to meet customer orders.
According to the company, the project has clearly had an impact on Waupaca’s operations. The workspace improved for workers, and the customers are happy with the product. The material and process flow is better thanks to efficient and accurate equipment locations and the new technology reduces variation throughout the coremaking process. The employees have workstations with better ergonomics, improved lighting and improved process controls.
“It shows what you can accomplish when you bring the best foundry team together, truly listen to concerns and suggestions, and seek out sound solutions.” said Dale Hardel, engineering manager, Waupaca. “Collectively we have demonstrated that safety and ergonomic improvements, energy efficiency, environmental awareness, and equipment innovation can be applied in a state of the art fashion to a classic foundry process.”
The project required strong collaboration with all involved. Waupaca engaged its vendors and suppliers early in the process by sharing design models and equipment requirements to provide for the most efficient construction process. Waupaca was able to engage team members across functions and departments to design an optimal workspace through Kaizen and benchmarking best practices.
Waupaca also had to battle a tight timeline, one that went right through the typically harsh Wisconsin winter. And it also had to figure out when to draw a line between what they wanted and needed to keep the project within budget.
Kimura Foundry America (Shelbyville, Indiana)
In August, AFS Corporate Member Kimura Foundry America (Schaumburg, Illinois) announced it was locating its first U.S. manufacturing facility in Shelbyville, Indiana. Kimura Foundry America is a subsidiary of Japanese company Kimura Group, and will invest $8 million into the facility, which was expected to open by December 2018.
Twenty new jobs will be created by 2020, and the company has bought a 10-acre parcel of land with plans to break ground in the fall for the plant, that will hold 3-D printing equipment. The facility will be important for Kimura’s production of complex castings and molds for automotive clients in the U.S., an area that is growing for the company.
With a project this important, it shouldn’t be surprising that Kimura painstakingly planned the move. Kimura Foundry America president Yoya Fukuda said the company coordinated with relevant companies and vendors about the technical information needed to start production.
The new building is a key part of Kimura’s strategy, and when it’s complete, it is expected to help it better serve its customers in the U.S.
It’s also part of the latest evolution for the company, which used an original evaporative casting process (ECP) for around half a century, and supplied mainly bigger castings such as parts for press dies, machine tools and industrial customers. The company went through a change in management in 2011, leading to a transition in strategy from ECP but also to a direct molding process that allowed them to produce more complicated castings in Japan, utilizing 3-D printing.
But this change also presented logistical challenges. Kimura tried to build relationships with customers to promote the direct molding process but had trouble keeping up with the growing demand from customers in the United States.
“That is why Kimura decided to build facilities to produce castings with the sophisticated 3-D-print technology in the U.S.,” Fukuda said.
To attract Kimura’s business, the Indiana Economic Development Corporation provided $225,000 in conditional tax credits and $25,000 more in training grants.
“Indiana is a global destination for companies from around the world looking for a place to locate, grow and add new jobs,” said Jim Schellinger, Indiana secretary of commerce. “Kimura’s decision continues a long trend of international companies, including many from Japan, choosing to make Indiana their U.S. home. Over the years, we’ve been fortunate to develop a close friendship with Japan, and we’re excited to welcome our friends at Kimura Foundry America to Indiana.”
Kamtek (Birmingham, Alabama)
Magna (Aurora, Ontario, Canada) recently cut the ribbon on the expansion of its Kamtek facility in Birmingham, Alabama, and is in the process of finalizing all of the equipment installations to meet customers’ requirements. Magna spent around $60 million to add the 150,000-sq. ft. facility that would generate more than 100 jobs at full capacity. The new facility will feature high-pressure diecasting and produce lightweight aluminum front shock towers for a major automaker, with more expected in the future.
“The expansion into this new arena of high-pressure diecasting for structural components has opened many doors for Kamtek and Magna,” Kamtek assistant general manager Rick Zimmermann said. “We now have the ability to provide full assemblies that include these high-strength structural aluminum castings.”
Zimmermann also passed along some valuable advice for companies looking to build similar additions.
“When undertaking a large project such as opening a greenfield site with new technology, one of the most important considerations is a common goal or to set the vision at the start of the project,” Zimmermann said. “Over the life of the project the team has to be flexible, and as items shift, even daily, the team needs to make decisions based on the vision and by keeping the end-goal in mind.”
Zimmermann said Magna worked closely with the local contractors and arranged for daily reviews of the plan vs. the actual progress to ensure the schedule was met. The first building column was set on Feb. 1, 2016, and Kamtek was running product at the end of June of that year.
“We had the right team and the right expertise that was needed to fulfill the requirements, and that is what made the difference in this project,” Zimmermann said.
Though it wasn’t the determining factor of the project’s success, the weather helped Magna finish the expansion on time. As Zimmermann pointed out, it doesn’t snow much in Birmingham, giving the company the advantage of working through the winter months.
“Conversely, the rain hindered our progress a little and we had to come up with solutions and work-arounds to maintain the schedule,” Zimmermann said.
But Mother Nature wasn’t the MVP. That was the Magna team.
“In all aspects of the project: leadership, engineering, quality, maintenance, and team members, working along with our support groups, we have achieved a common goal,” Zimmermann said. “Simply stated, teamwork was the success of this start up.”
The project’s full impact won’t be known until 2019 and 2020 but it is already having an effect.
“Our sister facilities have already utilized some of the innovations that we have completed here in Birmingham,” Zimmermann said. “We have successfully implemented a safer, more efficient and lean layout that benefits Magna worldwide.”
Sain Associates was involved with the architecture of the project, the IBI Group completed the building design, and Cooper Construction provided support on the construction manager side.
Brembo (Homer, Michigan)
Brembo celebrated the first pour of its 266,000-sq. ft. Homer, Michigan, iron casting facility in April 2016 and the foundry began its ramp up phase immediately after the equipment had been run off. The company is currently hiring the third and final shift for the foundry and by the beginning of the second quarter of 2018 should be running at full capacity.
And even though the facility is complete, Brembo is still facing the usual obstacles of a new facility.
“We are facing the typical challenges of a new plant (not just a foundry), in hiring and retaining the best people, training the foundry people of today and the future and making sure our new state of the art foundry equipment runs as expected throughout each day,” spokesman Dan Sandberg said. “Also, the dynamics of this foundry are interesting in that it is run by a multi-cultural management team, with expertise from the U.S., Poland, Mexico, China and Italy, of course.”
The Brembo foundry, which was an award-winning project for AFS Corporate Member Foundry Solutions & Design, was modeled after its other facilities across the globe, and having similar processes and equipment contributed to the company’s ability to ramp up at the plant. The management team’s prior experience starting new foundry lines was also helpful, but the road hasn’t been without some bumps.
“Of course, not all of our staff is as experienced with the state-of-the-art, specialized foundry process we have developed for the manufacture of brake discs, and even our seasoned staff had to become familiar with some improved processes and equipment we developed specifically for this new foundry,” Sandberg said. “We are going through somewhat of a typical learning curve.”
Brembo also encountered some challenges with a few of its equipment vendors. There has been some consolidation in the iron foundry business, which means fewer vendors that sell foundry equipment. And that unfortunate fact has been a challenge for Brembo as it builds its in-house foundry capacity for the future.
One area where Brembo benefited was the location.
“We believe that Michigan offered us a good workforce with a strong work ethic and technical skills,” Sandberg said. “It appears that our proven foundry processes and this experienced local workforce are coming together nicely.”
The new facility is already paying dividends for Brembo, as it gets close to half of its casting requirements from the facility that’s next door to its machining operations. It streamlines their product flow, eliminates transportation costs and other non-value-added movements.
“We are also able to fine-tune certain proprietary chemistries used by Brembo and our customers,” Sandberg said. “We also are able to better control our entire manufacturing process by having the casting, machining, coating and assembly processes all under one roof.”

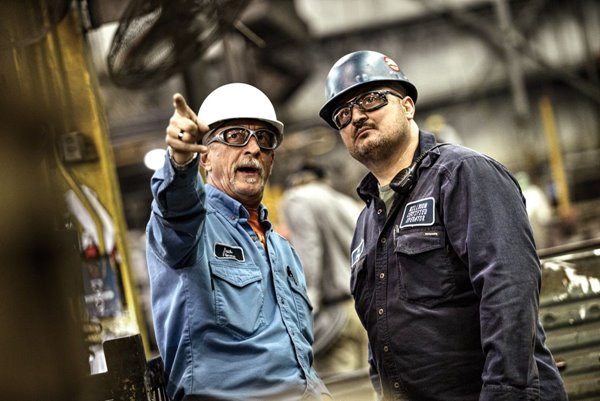