Foundry 4.0 and the future
Shannon Wetzel | Modern CastingThe metalcasting industry is going through its own version of a fourth revolution, and a growing number of suppliers, foundries, and end-users are creating new ways to use the internet of things to do their jobs more efficiently.
But what does Foundry 4.0 really mean?
“I would define Foundry 4.0 as anything to do with new emergent technologies, processes, procedure and systems, that have a socioeconomic impact on how foundries are currently operated,” said Hideki Gebken, engineering manager for Standard Manufacturers Services Limited (Winnipeg, Manitoba, Canada).
As a subset of Industry 4.0, Foundry 4.0 centers around smart manufacturing and what the future will hold with greater computing power, connectivity, feedback, and digitization of the physical world.
“I have always liked the concept that manufacturing is nothing more than imparting useful ‘shape information’ to a raw material,” said Randy Oehrlein, VP of engineering, Carley Foundry (Blaine, Minnesota). “In Foundry 4.0 we will encompass the technologies that make shape information move faster, more accurately, and with reduced physical effort as it is transformed into useful physical objects. In our industry’s case, that is metal castings and tooling."
Brian McCarthy, sales engineer, Versevo (Hartland, Wisconsin) points to how foundry pattern shops have been involved with digital manufacturing using CAD, CAM, and CNC technologies since the 1980s.
“We absorbed available technologies from other areas of manufacturing, and made it standard in our industry,” he said. “During the transition, the younger generation was getting a lot of pushback from the older generation. The next 10 years are going to be a similar situation as the younger generation thrives on technology and will be needed to replace the number of retirees in the next 10 years. In order for the metalcasting industry to attract the younger generation (and be competitive), there is going to be a need to absorb some of the advanced manufacturing options available today that are being utilized in other industries.”
Foundry 4.0 includes many aspects, including the use of robotics, artificial intelligence, data and process automation, and other emerging technologies. But it also encompasses how digital manufacturing will affect the way employees engage with each other, the machinery and customers.
“Foundry 4.0 forces us to think about the future: what are the future demographics that will affect our industry, how will changing transportation trends affect the type of castings we make, what new regulations will need to be considered in our operations, what new energy sources will be incorporated in our business?” said David Weiss, VP of engineering and development, Eck Industries (Manitowoc, Wisconsin). “As the rate of change increases and as advanced technologies become ubiquitous, how can we use those tools to create a profitable, sustainable foundry businesses that can operate far into the future?”
A conference that looks at the various ways current and emerging technologies can be applied by metalcasters is scheduled for June 9-10 in Itasca, Illinois. Put together by the American Foundry Society and members of its various committees, the Foundry 4.0 Conference will cover key topics like data collection and management, data-driven decision-making, artificial intelligence, augmented reality, virtual reality, wearable technology, robotics, automation, and cyber security, as well as the related issues of workforce development, recruiting, and training. The conference will include foundry case studies demonstrating how implementation of data collection, automation, and digital technologies have changed and improved operations today. More information on the conference is available at www.afsinc.org/conferences/foundry-40.

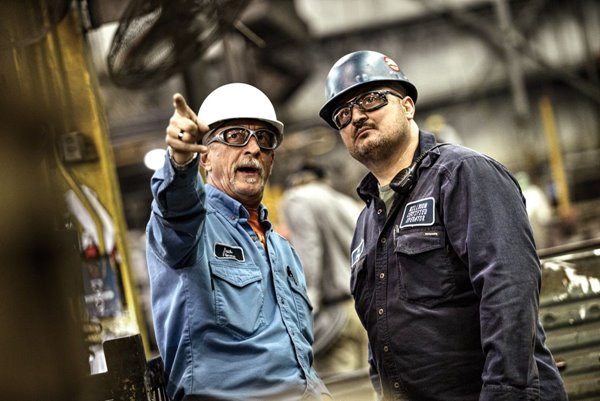