“It was a huge advantage having someone internal who is very familiar with the project, especially Kris and his team,” Jezwinski said.
Gate and Spure Conveyor Improves Plant 4 Uptime, Workplace
Mary Schmidt | Waupaca FoundryWaupaca Foundry engineering and maintenance teams complete capital project in under two weeks over holiday shutdown
The task was clear: the Plant 4 engineering and maintenance teams were to upgrade the shaker system that transports ductile iron casting gates and sprues in two weeks over the 2023 holiday shutdown.
In-house engineering and maintenance teams began planning for the capital project in 2022 with the objective of tackling all the identified challenges associated with equipment, including material congestion, noise, dust generation, downtime, and rising costs.
Planning started in 2022. The capital project required months of meticulous planning from internal engineering teams to reduce downtime, enhance production efficiency, and improve worker safety and health. Jarrod Osborn, vice president of manufacturing engineering for Waupaca Foundry, emphasized the importance of preparation and planning in anticipation of the project. This was particularly crucial due to the extensive scope of work involved, especially within the defined shutdown and installation window.
The original vibratory shaker system at Waupaca Foundry was installed in 1992, more than 30 years ago. The system is downstream from six ductile iron casting molding lines and is responsible for separating and transporting gate and sprue material to the charge yard for reuse. However, the equipment had reached the end of its life and could no longer keep up with demand.
The system faced frequent jams caused by gates and sprues. These jams were particularly problematic because when congestion occurred near a line, it would bring production to a halt, which was continuative to uptime and delivery. The legacy shaker system was loud, and the vibration to transport the gate and sprue material kicked up dust from the greensand mold in the ductile iron shakeout area. Moreover, the shaker's placement in a pit beneath all six production lines presented challenges for maintenance teams due to barriers to accessibility and confined spaces.
Relocating two DIDION Rotary Media Drums® was just one of nearly 300 action item identified to complete the capital project.
After extensive investigation, multiple site visits, and thorough planning, the solution was to replace the existing vibratory system with two parallel Superbelt conveyor systems from Magaldi. Unlike the vibrating system, the new conveyor system is designed to move materials gently at varying speeds.
But the transition wasn't as straightforward as simply removing one piece of equipment and installing a new one in the same space. According to Rob Jezwinski, “We had the option to cram the new system in the existing space, but working on it would have been a nightmare.”
With the implementation of the new conveyor system, Waupaca Foundry seized the opportunity to provide its maintenance team with space to efficiently and comfortably carry out equipment-related tasks as required.
The engineering team, led by Engineering Managers Kris Olynick and Rob Jezwinski, meticulously identified nearly 300 action items in its installation plan and initiated the capital project by generating 3-D scans of the existing area. These scans proved the most critical advantage in seamlessly fitting the new conveyor system into the existing plant footprint.
“When we started this project, there were no models, and very little documentation at all on the equipment and building layout,” Kris Olynick, project engineer. “We spent a lot of time in the plant modeling and building a 3-D model of the area from nothing.” The scans were used to plan the new equipment layout, existing equipment modifications, building modifications, installation access points, and determine fits between equipment.
“Scott Fielding and I spent countless hours pouring over the details of this project,” Olynick said. “We meticulously identified steps, identified pitfalls of each step, measured and remeasured, planned any prework we could to remove labor from the installation, and walked through every single step of the process multiple times.”
To meet the installation goal, Olynick, Jezwinski, and team made major renovations to the space inside the plant:
-
The removal of the legacy equipment involved cutting access points into the pit to demolish existing concrete.
-
Two DIDION Rotary Media Drums® were relocated.
-
Conduit locations and ductwork were repositioned to accommodate the new system.
-
Arriving from Italy, the conveyor system was transported in 15 40-foot shipping containers in late November of 2023.
-
The new system was staged outside in order to be installed despite the challenging weather conditions.
Brandon Kruse, general manager of Magaldi Technologies, was on site for most of the installation. He said that having in-house engineers made a big difference in planning and installing the new system in this short timeframe.
“Kris spent every other weekend at the plant for a good part of the year planning out column relocations, relocations for conduit, pipework, ductwork, sand conveyors, and everything you could imagine,” Kruse said.
The Magaldi Superbelt conveyor system was identified as the best solution because the conveyor belt used to move the gate and sprue material has a sensor that tracks scrap height to control the speed of the belt. And, because the system is not vibrating, it reduces noise and dust in the work area, creating a safer working environment for team members.
“All that goes away because you’re not banging castings against a vibrating conveyor deck,” Kruse said.
The new system is anticipated to reduce maintenance downtime in the shakeout area by as much as 50% and is estimated to offset rising maintenance and energy costs. But more important than the bottom line is the system will improve the work environment by decreasing noise and dust and allowing maintenance teams safer, easier access to the conveyor.
The new system is expected to significantly reduce conveyor maintenance downtime by up to 50%, offsetting rising maintenance and energy costs. Beyond financial benefits, the system will profoundly impact environmental health and safety (EHS) with decreased noise and dust levels. Additionally, it will provide safer and easier access to the conveyor, further contributing to improved working conditions and operational efficiency for maintenance.

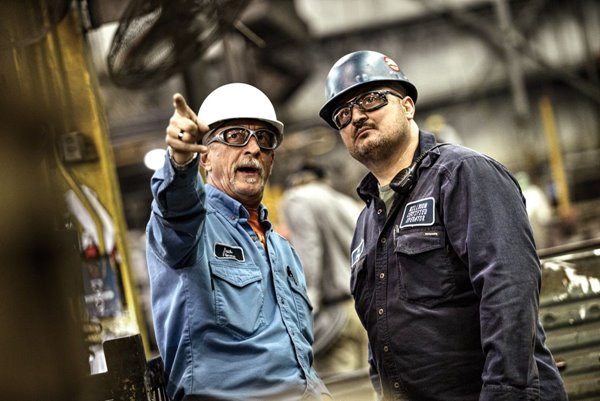