The quest for quality castings drives Waupaca Foundry to constantly seek out improvement opportunities. To this end, the core assembly and Waupaca Way teams examine foundry processes, adhesives, jigs, designs, and whatever else it takes to establish a new—and better—best practice.
Improving the Quality of Castings at Waupaca Foundry
Scott Bailey | Waupaca FoundryMost of the gray iron castings part numbers targeted for improvement are driven by a desire to reduce scrap numbers. Yet we also tackle jobs that have decent scrap numbers, but might flow inefficiently through the core room, or jobs that may present safety risks.
Changing a gray iron casting core assembly is just one example of how addressing ergonomics and safety also reduced scrap and improved quality.
Gray Iron Casting Assembly Improvement
After conducting an ergonomic risk assessment, we identified a core assembly for a gray iron casting (water pump housing) having an ergonomic ranking of 30. Ergonomic rankings of 10 are considered very good, while 20 would be an average. Thirty is too high to be considered safe. The part's cores were run first and then had to be assembled offline, which contributed to the elevated ranking.
To assemble the core for this gray iron casting, a very large, heavy jig was used. The core was manually assembled upside down using screws and glue. Next, the operator then had to manually and very carefully lift the heavy core assembly straight up in a perfect manner to ensure that it wouldn't crack or break. At 49 pounds, this was a cumbersome undertaking. It required awkward bending, as well as extreme physical exertion of the back and arms, creating a potential for injury.
Additionally, because of this difficulty, cores were commonly broken, resulting in 10% scrap from assembly related issues.
The core assembly for the gray iron water pump housing was uncomfortable to assemble and impeded worker ergonomics; and it also had a higher scrap rate affecting casting quality. Acknowledging this, the process to assemble the cores into a single unit was reinvented.
The new process uses the base core as a jig whereby hoist pockets were cut into the base core to allow a hoist hook to safely lift the heavy assembly. We changed bosses to glue pockets and added glue pockets, as well as added blown-in pins to assist in guiding placement and assembly.
Altogether, borescoping was eliminated, the need to install screws in the assembly was eliminated, and the assembly is now performed upright, eliminating the need to flip the heavy assembly. Additionally, the core base now has hook pockets to allow a hoist hook to help safely lift the heavy assembly.
The Results
This core assembly process change has led to a safer assembly, more efficient production, and higher quality castings. The new ergonomic ranking for the part and assembly is now a 10 instead of 30. And in just one year, we've also cut the scrap fallout in half, from 10.4% to 4.8%.
We continue to refine and adjust not only our core making process, but all gray iron casting foundry processes to keep both safety and casting quality our priorities.

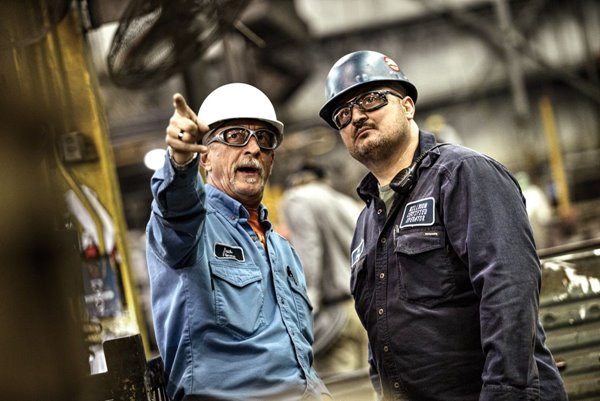