New Soft Exoskeleton Glove in Foundry Lends a Hand to Worker Wellbeing
Ally Melby | Waupaca FoundryIronhand® Bridges Waupaca Foundry’s Journey to Automation
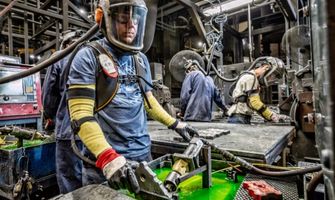
Marinette employee wearing the Ironhand
Today’s casting cleaning and finishing features a blend of technologies and manual operations to process and inspect iron castings. For those manual tasks, one of the greatest challenges workers face is fatigue in their hands. The Ironhand is designed to improve grip strength, allowing operators to use less force when performing repetitive tasks and reduce exertion on the body.
“Employee feedback has been positive. We have one employee that opted out of the trial as a new hire, and within a couple of weeks of being out on the floor, the employee requested to be put back in the trial,” says Cory Haberland, Waupaca Foundry safety manager at its Plant 4 ductile iron foundry located in Marinette, Wisconsin.
“When holding the grinder for a long period of time or lifting and holding large parts, it helps tremendously,” says Joey Slater, a millroom grinder.
Weighing only six pounds, the Ironhand system is a power pack worn in a backpack or hip-carry and integrated with a worker’s existing personal protective equipment. The technology looks like a regular glove but is equipped with artificial tendons and pressure-sensitive sensors to mimic the human hand. Through the Smart Assist function, the glove can be adjusted according to the user’s preferences and work situation.
“I can already tell that my hands are less tense when I wake up and less sore at the end of the day. The gloves took some time to get used to,” says Trever Godfrey, a millroom grinder, “But then the gloves learned what I was doing, and it had definitely made a difference.”
“One of the big benefits we're seeing out of Ironhand is that we believe it's going to improve employee retention. There's a safety factor to having employees that stick around. It’s not just a financial investment, but there's a skill set there that we can't easily replace when we have high levels of turnover,” says Jon Loken, director of health and safety.
The Ironhand is a development of Swedish company, Bioservo Technologies. Waupaca Foundry and Bioservo Technologies are working in partnership to create a glove specifically built to withstand a foundry’s work environment.
Currently, 30 Ironhand systems are being tested at Waupaca Foundry Plant 4 in Marinette, Wisconsin and Plant 6 in Etowah, Tennessee. Bioservo Technologies is continuing to improve the system during the product testing phase through employee and product feedback.
The introduction of the Ironhand in the mill room is just the beginning. Following a 6-month trial and adjustment period, Waupaca Foundry employees can expect the Ironhand system to be implemented at all plant locations with expansion to other departments, such as molding and the core room.
“Automation is not something that can be completed overnight. It takes time and capital. The Ironhand glove will fill the gap until further automation can be put in place,” Haberland says.

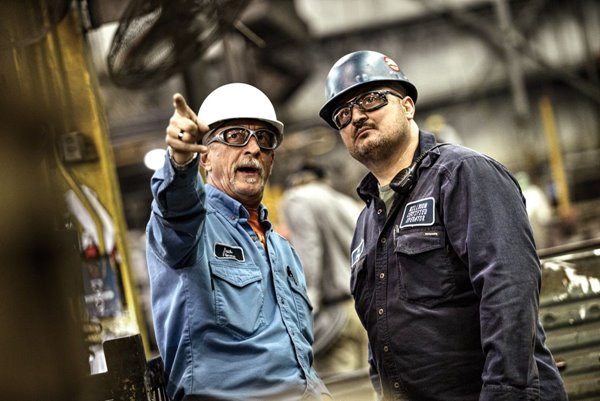
We use cookies and other tracking technologies to personalize content and analyze our site traffic. More information about this is in our Privacy Policy. You can control third party cookies by adjusting your browser settings.