Ironhand® Exoskeleton Protects Foundry Workers

Ironhand® Exoskeleton Protects Foundry Workers
WAUPACA, Wisc. — Waupaca Foundry is using an innovative adaptive technology to support workers who manually grind iron castings in the foundry. The Ironhand® glove is the world’s first soft exoskeleton designed for the human hand to improve grip strength and reduce effort. The system was tested at the iron casting supplier’s Etowah, Tenn. casting finishing plant and is currently in trials at the Marinette, Wisc. ductile iron foundry.
The system consists of a glove covering all five fingers, and a power pack worn in a backpack or hip-carry. It is activated when the operator starts moving his/her hand to perform a task, using sensors located on the palm and on the fingers.
Via the Smart Assist function, the system learns how each operator uses the glove and adapts the control system to provide a natural force. The entire system weighs just 6 pounds and is integrated with existing personal protective equipment.
Currently, 30 of the Ironhand systems are in use at two Waupaca Foundry operations and foundry team members report the system supports their bodies, is comfortable, and is easy to operate.
The glove is used most often in the casting grinding and press functions of the foundry where workers are performing repetitive tasks and lifting castings. The iron casting supplier plans to expand the use of Ironhand to additional foundry functions such as in the molding and core room departments.
“For the last 25 years, we have improved technology with the goal to eliminate manual casting processing, but we cannot eliminate handling iron castings as part of our daily jobs,” said Jon Loken, director of safety and health. “This technology bridges the gap between manual processing and total automation.”
“The iron hand works well for holding onto air tools for an extended period of time,” said Andrew Lang, a grinding operator in the mill room at Waupaca Foundry.
“I had to see what it was all about, so I said I wanted to try it,’ said Trever Godfrey, a millroom grinder. “It makes a big difference because the glove takes over and does most of the work for you. It also took quite a bit of the vibration out of my arm.”
“Feedback from our employees is outstanding,” Loken said. “It’s better than imagined and this is one more step in our goal to improve ergonomics and the overall work environment for our team.”
The Ironhand was developed by a Swedish company, Bioservo Technologies. The technology is in use in different manufacturing sectors, but the foundry environment provided unique challenges.
Specifically, iron dust in the mill room was penetrating the gloves and connections, so insulation on the cables was enhanced. The company is continuing to improve the system during the product testing phase.
“The application with Waupaca Foundry opens new possibilities for Ironhand to truly make a difference for people in their daily work life within a large and demanding industry. The initial results show that a majority of workers who tested Ironhand want to use it in their daily work to stay healthy,” said Petter Bäckgren, CEO of Bioservo.
The system is being distributed by Rhino Tool House, which is supporting installations at multiple Waupaca locations throughout the Midwest and working with Bioservo to monitor the results.
“This is a product we are very excited about and we have deployed this in various production environments around the country,” said Chip Paulsen, president of distribution. “Everything from automotive factories, aerospace plants, warehousing, fabrication shops and now foundries are using the technology.”
Following a 6-month trial and adjustment period, the Ironhand system will be implemented at all Waupaca Foundry locations. The partnership’s objective is to develop a long-lasting glove for use in both foundry and machining operations.

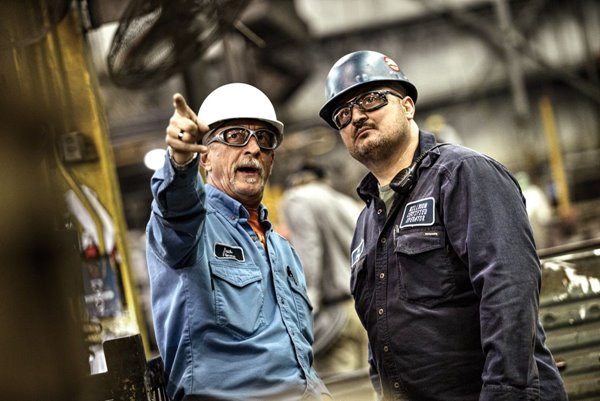