Light Weighting ... or Right Weighting?
Paul Jones | Waupaca Foundry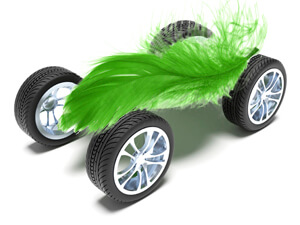
Here at Waupaca Foundry, we love the camaraderie that accompanies the challenges presented by our customers. We take pride and satisfaction in working with our customers to create a product that fits their needs.
In the past 30 years, the domestic auto industry has been determined to achieve government and consumer-driven fuel economy improvements. This has resulted in a great deal of material conversions from iron and steel to lightweight materials such as aluminum and other metals. Weight reduction has gotten so popular, in fact, it has recently become known as “light weighting.”
From an engineering perspective, the tactic of “light weighting” seems limiting. From a business perspective it seems undesirable. If the auto industry goal is to improve fuel economy while optimizing costs and consumer prices, it seems that a well-driven business and engineering approach is most desirable. At Waupaca Foundry, we think of this as “right weighting.” We take fundamental and leading technology and combine them with sound business planning to achieve the most positive impact on our customer. This combination of Waupaca’s expertise and the customers’ expertise and willingness to improve their product makes for successful partnerships.
What we do at Waupaca is fundamentally sound, business-driven, and applies technology wisely. Keeping people safe is our most important mission, but we also believe in finding the best way of doing things. We know that the mix of increased strength, toughness, and percent-elongation options of our materials when combined with the stiffness of iron provides advantages relative to some lighter weight materials. Collaborative iron casting designs that optimize material grade selection and casting fill and solidification criteria provide robust solutions to customer requirements. This means that the more dense iron material does not have to result in designs whose weight is vastly different than lightweight material designs.
We know driveline systems that use a lightweight and less stiff aluminum design often require the addition of NVH-driven tuned mass dampers. Lightweight components by definition may be lighter. But the mass reduction of the component may be offset by the addition of tuned dampers to the assembly.
We know that iron material costs are less than lightweight material costs. We are eager to combine cost effectiveness with effective designs to help our customer save money without jeopardizing (and actually improving) functionality, quality, and safety. These practices are long standing and we intend to keep them so.
“Right weighting” is an exciting opportunity for current and prospective customers, and it’s an opening to a bright future. Talk to your casting supplier about focusing on mass optimization while preserving performance. Please contact us so we can collaboratively achieve designs that tackle the challenges of improving vehicle fuel economy.
In the past 30 years, the domestic auto industry has been determined to achieve government and consumer-driven fuel economy improvements. This has resulted in a great deal of material conversions from iron and steel to lightweight materials such as aluminum and other metals. Weight reduction has gotten so popular, in fact, it has recently become known as “light weighting.”
From an engineering perspective, the tactic of “light weighting” seems limiting. From a business perspective it seems undesirable. If the auto industry goal is to improve fuel economy while optimizing costs and consumer prices, it seems that a well-driven business and engineering approach is most desirable. At Waupaca Foundry, we think of this as “right weighting.” We take fundamental and leading technology and combine them with sound business planning to achieve the most positive impact on our customer. This combination of Waupaca’s expertise and the customers’ expertise and willingness to improve their product makes for successful partnerships.
What we do at Waupaca is fundamentally sound, business-driven, and applies technology wisely. Keeping people safe is our most important mission, but we also believe in finding the best way of doing things. We know that the mix of increased strength, toughness, and percent-elongation options of our materials when combined with the stiffness of iron provides advantages relative to some lighter weight materials. Collaborative iron casting designs that optimize material grade selection and casting fill and solidification criteria provide robust solutions to customer requirements. This means that the more dense iron material does not have to result in designs whose weight is vastly different than lightweight material designs.
We know driveline systems that use a lightweight and less stiff aluminum design often require the addition of NVH-driven tuned mass dampers. Lightweight components by definition may be lighter. But the mass reduction of the component may be offset by the addition of tuned dampers to the assembly.
We know that iron material costs are less than lightweight material costs. We are eager to combine cost effectiveness with effective designs to help our customer save money without jeopardizing (and actually improving) functionality, quality, and safety. These practices are long standing and we intend to keep them so.
“Right weighting” is an exciting opportunity for current and prospective customers, and it’s an opening to a bright future. Talk to your casting supplier about focusing on mass optimization while preserving performance. Please contact us so we can collaboratively achieve designs that tackle the challenges of improving vehicle fuel economy.

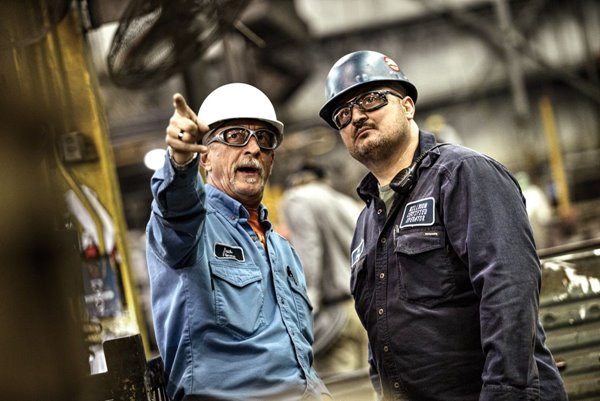
Have a lightweighting, casting conversion, reshoring or other initiative to discuss?
Contact Us
We use cookies and other tracking technologies to personalize content and analyze our site traffic. More information about this is in our Privacy Policy. You can control third party cookies by adjusting your browser settings.