Mike Nikolai Receives Sustainable Leadership Award
Halden Collins | Waupaca FoundryWaupaca Foundry is running a 50% reduced scrap rate in 2015 at Plant 1 located in Waupaca, Wisconsin. Read how continuous improvement, employee ingenuity and an investment in quality made this happen.
Molten metal filters are used in the iron casting process to prevent slag and other harmful inclusions from entering the mold and ending up in the final casting. There are several types of molten metal filters to choose from. However, to guarantee the best performance from any filter, it is critical to have an understanding of the physical characteristics of the slag or inclusions specific to your foundry application.
About three years ago, Waupaca Foundry's Plant 1 located in Waupaca, Wisconsin set to select the right molten metal filter. On all of the gray iron casting lines, Waupaca introduced a more expensive filter into the iron casting pouring process after a year's worth of trials.
Waupaca Foundry was noticing a sizable increase in scrap on one of its lines. The line would be run for 2-3 hours and then the scrap rate would start to increase. At a Waupaca Way Production System level 4 meeting with its process engineering team, a group of engineers dedicated to continuous improvement, a molding foreman, Dave Peterson recommended changing the filter type to decrease the melt contaminants and reduce the scrap rate. The process engineering team took this suggestion to heart and received permission to run trials after some convincing arguments were presented. At the end of the first year of trials, Waupaca Foundry had increased the filtration of the melt to decrease the inclusions which resulted in a 40% reduction in scrap. To date in 2015, the scrap rate is now running 50% lower than before the filter switch was implemented. All vertical molding lines are running with the new filter type based on the foreman's initial recommendation. Changing the filter resulted in an investment of roughly $120,000.00 that Waupaca Foundry felt they had to make to increase casting quality. The reduction in scrap helped to offset rising material and other operational costs.
Although a great deal of promising research on improving molten metal filtration technology and efficiency continues in both industry and academia, the vast majority of currently available molten metal filters rely on their relative "sieving" or "screening" ability to remove slag and other inclusions from the base metal as it passes through the body of the filter. It is worth noting that there really is no "perfect" or one-size-fits-all molten metal filter. Each has its own strengths and weaknesses that need to be considered carefully.
Selecting the Right Filter
The surface area of the molten metal filter should be at least six times the cross sectional area of the ingate. Pore size is measured in pores per square inch (ppi). Three main pour sizes can be used – 10 ppi (course), 15 ppi (medium) and 25 ppi (fine). Pore size selection is slightly different for each type of metal cast, but the main factors to consider before choosing a pore size include:
- Melt cleanliness prior to filtration,
- Casting cleanliness requirements,
- Available space or pattern equipment, and
- Metal flow rate requirements.
For most grey iron foundry applications, 15 ppi filters are adequate. Ductile iron melts tend to have a significant amount of dross due to metal treatment. 10 ppi or 15 ppi filters satisfy most ductile iron casting applications.
The important characteristics of filters are filterability and freeze avoidance. 'Filterability' means that the filter must do its job, i.e. take out from the melt inclusions which would otherwise result in scrap castings or castings which would require substantial and costly reworking. 'Freeze avoidance' means that the filter must allow the passage of liquid steel through the filter without allowing the molten metal to freeze in route, causing misrun castings.
The best filter is the one that meets or exceeds your application requirements and is reasonably priced. In general, the more required of the filter the higher the cost. In instances where the end-casting will be a critical high-performance item such as a medical implant or a turbine blade, and even minute imperfections are unacceptable, the cost of the filter becomes far less important than its ability to remove inclusions.

MOLTEN METAL FILTER TYPES: Aluminum filtration fiberglass mesh filter High silica fiberglass mesh filters for iron and small scale steel castings filtration Ceramic extruded filters for aluminum and iron filtration Alumina ceramic foam filters for aluminum filtration SIC ceramic foam filters for iron and non-ferrous castings filtration
With molten metal filters, the following needs to be taken into consideration:
- The removal of harmful inclusions.
- The physical characteristics of these inclusions.
- The pouring temperature.
- The critical nature of the end cast part in the field.
Choosing the right molten metal filter takes trial and error. These trial runs are time consuming and costly, and in most cases the resulting best molten metal filter will also add cost to the overall manufacturing process in the long run. With all of these obstacles being a challenge to both plant and upper management, setting out on a journey of this scale takes a great deal of thought and commitment.
This change in Waupaca Foundry's molten metal filtration process ultimately helped both the gray iron casting foundry and its customers by:
- Increasing Efficiency
- Lowering Manufacturing Costs
- Improving the quality of the castings
- Helping with the on time delivery of product.
It is this type of continuous improvement that drives Waupaca Foundry to be a high quality gray iron and ductile iron casting manufacturer.

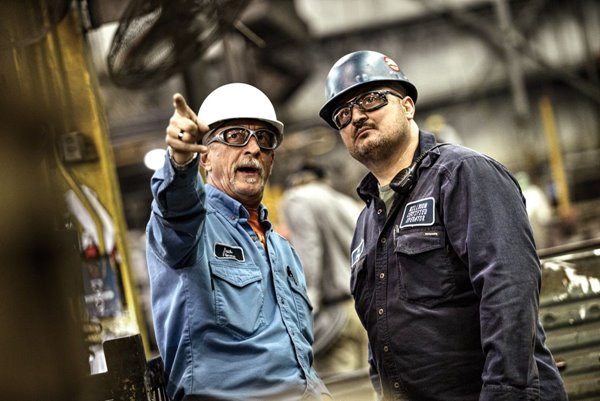