Ricardo-Designed Ultra-Lightweight Driveline System
Details of Ricardo-designed ultra-lightweight driveline systems to be revealed at CTI Berlin
- The internal layout of an innovative rear drive unit, designed and manufactured in prototype form by Ricardo, will be revealed for the first time today at the CTI Symposium
- This ultra-lightweight prototype saves a full 8.5 kg (24 percent) in comparison with that of the baseline production vehicle
- Also on show will be a Ricardo designed multi-material manual transmission casing prototype saving 1.9 kg (16 percent)
- These ultra-lightweight concepts were engineered as part of the recently completed Ultra-Lightweight Transmission and Driveline (ULTRAN) collaborative research project
ULTRAN has been a three-year research initiative led by Jaguar Land Rover in a consortium including Ricardo, Tata Steel, Lubrizol, GRM Consulting Ltd, American Axle & Manufacturing and the Universities of Southampton, Newcastle and Warwick – with the support of the UK’s innovation agency, InnovateUK. The project set out to accelerate the processes of designing, developing and validating cost-effective lightweight drivetrain technologies, aiming to significantly push forward the practical application of reducing the mass of driveline systems and components. The latest generation Range Rover was the baseline for the research – a vehicle already the subject of extreme mass reduction, being 16 percent lighter than its predecessor.
Ricardo led the concept generation through to the manufacture and testing of the ultra-lightweight rear drive unit, which was a major focus of the ULTRAN project. A fully clean sheet design with a Ricardo patent pending, the unit is based around a lightweight differential mounted within an innovative, compact, single-piece skeletal casing with tough, low-density lightweight plastic covers. The form of the skeletal design originated from finite element-based simulation and topology optimization. Using this data-driven template, the skeletal design could then be developed in CAD, based on a single integrated aluminium die-cast structure, with closures and fluid seals formed by the lightweight plastic cover assemblies. Using its systems approach to lightweighting, Ricardo eliminated internal parts and simplified those remaining, while maintaining comparable performance or improving upon the baseline design. The conventional differential carrier has been eliminated with the crownwheel supported in a double-row angular contact bearing, and differential gears supported directly within the crown wheel. A hollow pinion shaft was designed and manufactured, delivering a mass saving of 1kg for this component alone. The overall 8.5 kg (24 percent) mass saving of the complete unit was achieved approximately equally between the gears and shafts, and the casing system.
The TRL-5 prototypes of the rear drive unit manufactured by the project have been thoroughly evaluated under tests including high torque (5000 Nm), lubrication tilt, efficiency, durability (including extreme duty cycle) and in-vehicle ride and NVH. Through these evaluations, the prototype unit demonstrated its functionality with comparable performance to the current production unit.
Ricardo’s systems approach to lightweighting was also demonstrated with the design using similar processes, of a 6-speed manual transmission casing. In this instance, in a design also the subject of a Ricardo patent application, a weight saving of 1.9 Kg (16 percent) was achieved in comparison with the baseline.
“The Ricardo contribution to the ULTRAN project has demonstrated the very significant opportunities for driveline lightweighting that can be realized when a systems approach to product design for mass optimization, is applied by our highly experienced and creative engineers,” commented Ulf Herlin, head of the Ricardo Driveline and Transmission Systems Product Group. “ULTRAN set very ambitious goals by defining as its baseline vehicle a product that in many respects represents the current state of the art in terms of driveline mass reduction. By applying the methodologies demonstrated in the ULTRAN project, we have shown that significant further mass reductions – with consequent improvements in vehicle efficiency and CO2 savings – are possible at comparable cost and performance to existing production, based on market-ready materials, processes and design technologies.”
The ULTRAN rear drive unit and transmission casing are both on display at the Ricardo exhibition stand J06 at the CTI Symposium, Berlin. The paper 24% mass reduction from light-weighting process applied to an axle describing the design of the ULTRAN rear drive unit, will be presented at 2pm today.

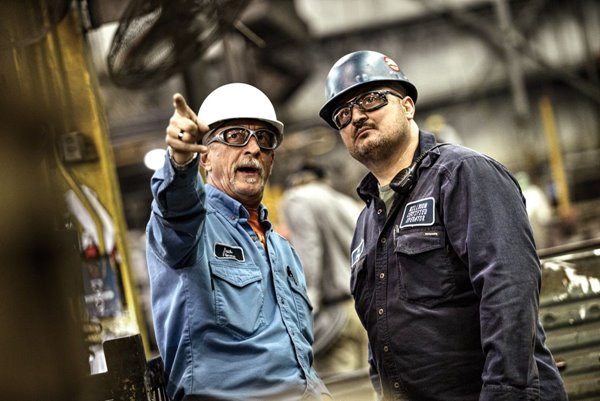