Recycling and reusing is not a new idea for the foundry industry. But bringing used foundry by-products back into the molding and casting process... That's news. In February 2013, Waupaca Foundry will be the first in the United States to install state-of-the-art sand reclamation technology at Plant 2/3 to reclaim used sand for the foundry. This experimental pilot program will bring new value to old sand and help reduce Waupaca's dependence on new-sand purchases.
Technology Gives Old Materials New Life
Bryant Esch | Waupaca FoundryUntil now, Waupaca's used foundry sand has been incorporated as construction material for off-site projects. The City of Waupaca's new sledding hill at the Swan Park Recreation Facility is one example of reused fill. But the greatest value of used foundry sand is reclaiming it and reintroducing it back into the casting process.
The new sand reclamation technology sorts, heats and separates used foundry sand. First, used foundry sand is mechanically sorted to obtain the reclaimable sand. Then it is placed into the Thermal Reclaimer where it is heated to over 1,300 degrees Fahrenheit. The extreme heat forces clays and resins, created during the initial casting process, to "pop off" the sand particles, leaving behind usable sand. The sand is mechanically separated once more to ensure that only usable reclaimed sand makes its way back into the process.
Looking at this new environmental and sustainable initiative from both sides of the coin: Waupaca Foundry is generating less solid waste, yet using more energy to operate the thermal reclaimer. That said, initial calculations of this pilot program show that the reclamation technology will make up for itself both environmentally and in overall savings as compared to current sand handling practices.Extensive testing and benchmarking will take place at Plants 2/3 in Waupaca, Wisconsin, with the intention of extending this technology to other plants in coming years.

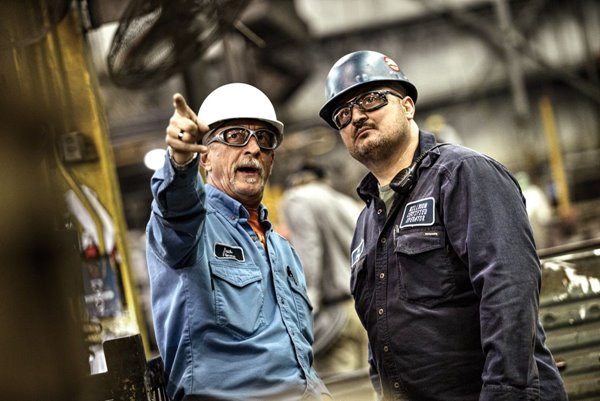