Accelerate Your Iron Casting Launch With Waupaca Foundry
Megan Mulholland | Waupaca FoundryAccelerate Development. Reduce Risk. Gain Competitive Advantage.
Waupaca Foundry offers five in-house rapid prototyping solutions, a capability few foundries in North America match. In-house rapid prototyping, reduces complexity and delays from third-party vendors enables tighter communication, better process control, and improved lead times. Waupaca’s prototyping uses the same processes and materials as full-scale production and results in consistent, reliable iron casting quality—ideal for functional testing or limited production.
Our vertically integrated approach delivers what matters most to you:
- Speed to market
- Early Design Validation & Risk Reduction
- Production-ready quality
Choose the Prototyping Solution for Your Timeline, Budget, and Goals.
Normal Prototype Pattern & Core Box
The pattern and core box are made from soft tooling materials with fewer cavities, allowing flexibility to run multiple part numbers on the same pattern. Castings are produced using the standard production process for consistent quality.
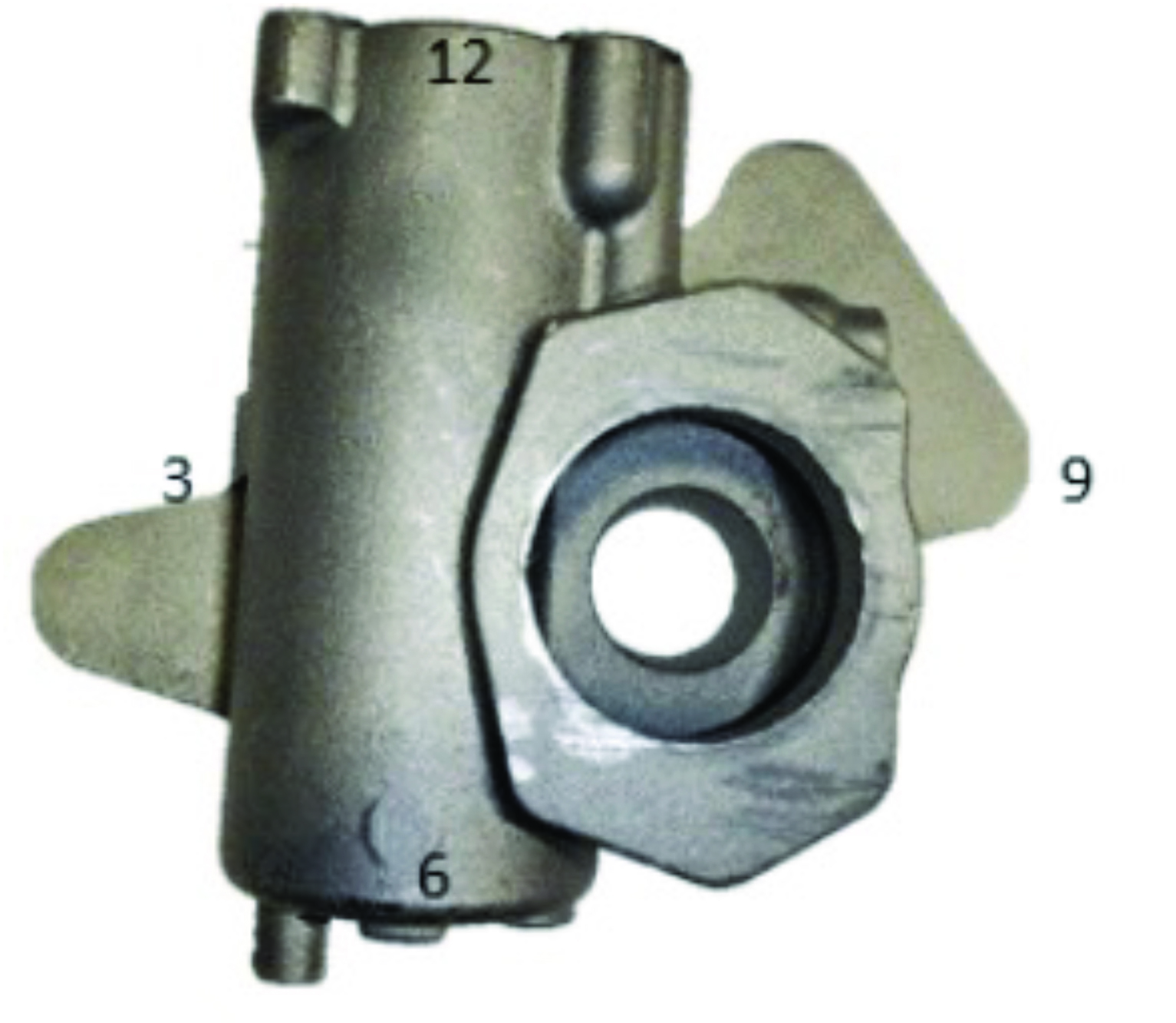.jpg)
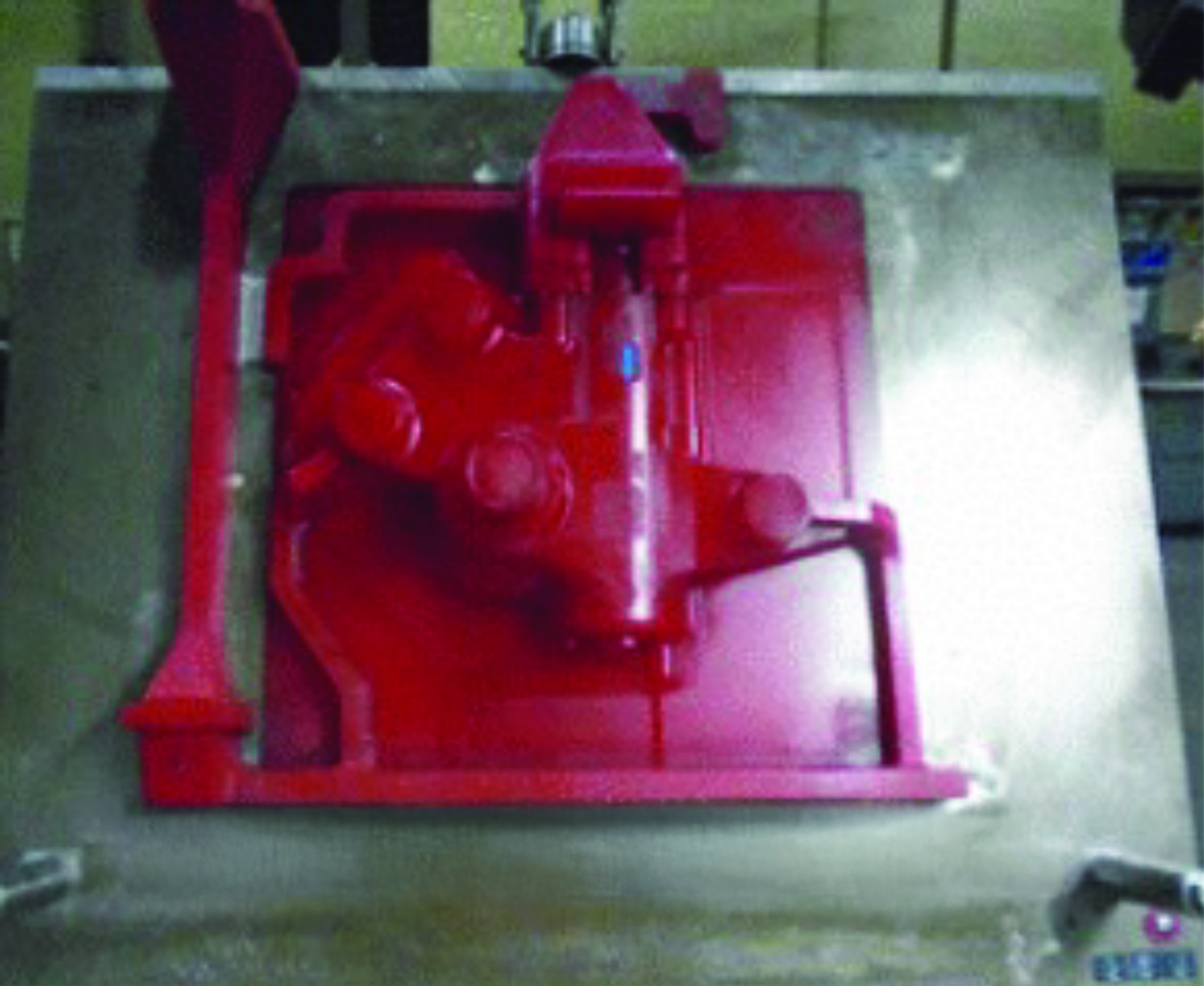
- Piece Cost: Low
- Lead Time: 8-14 weeks
- Quantity: 50-1,000+ pieces
Normal Prototype Pattern & 3D-Printed Core
A soft tooling pattern with fewer cavities is combined with a 3D-printed core, significantly reducing lead time. This method allows multiple part numbers to run on the same pattern, with castings produced using Waupaca’s standard production process.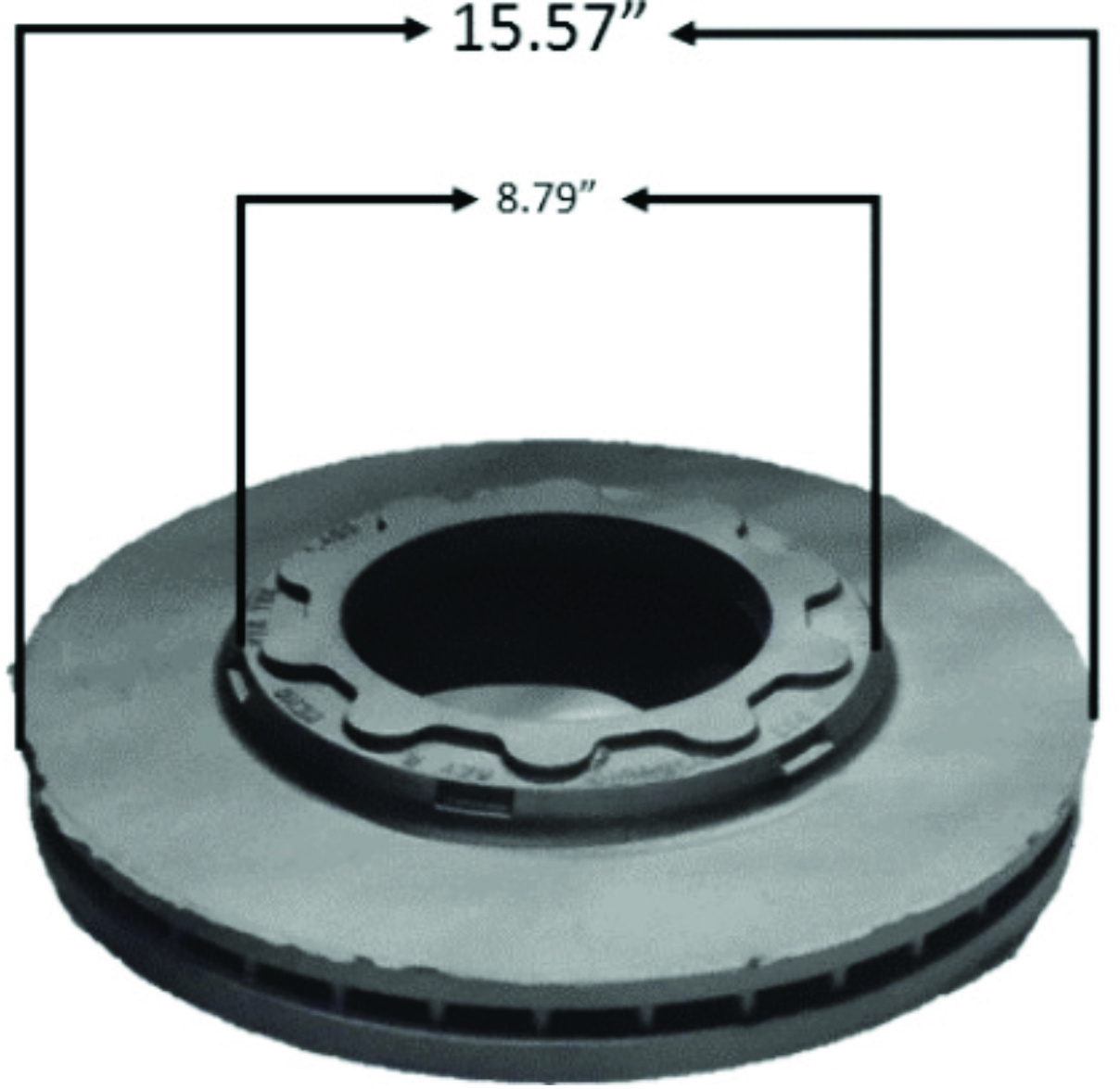
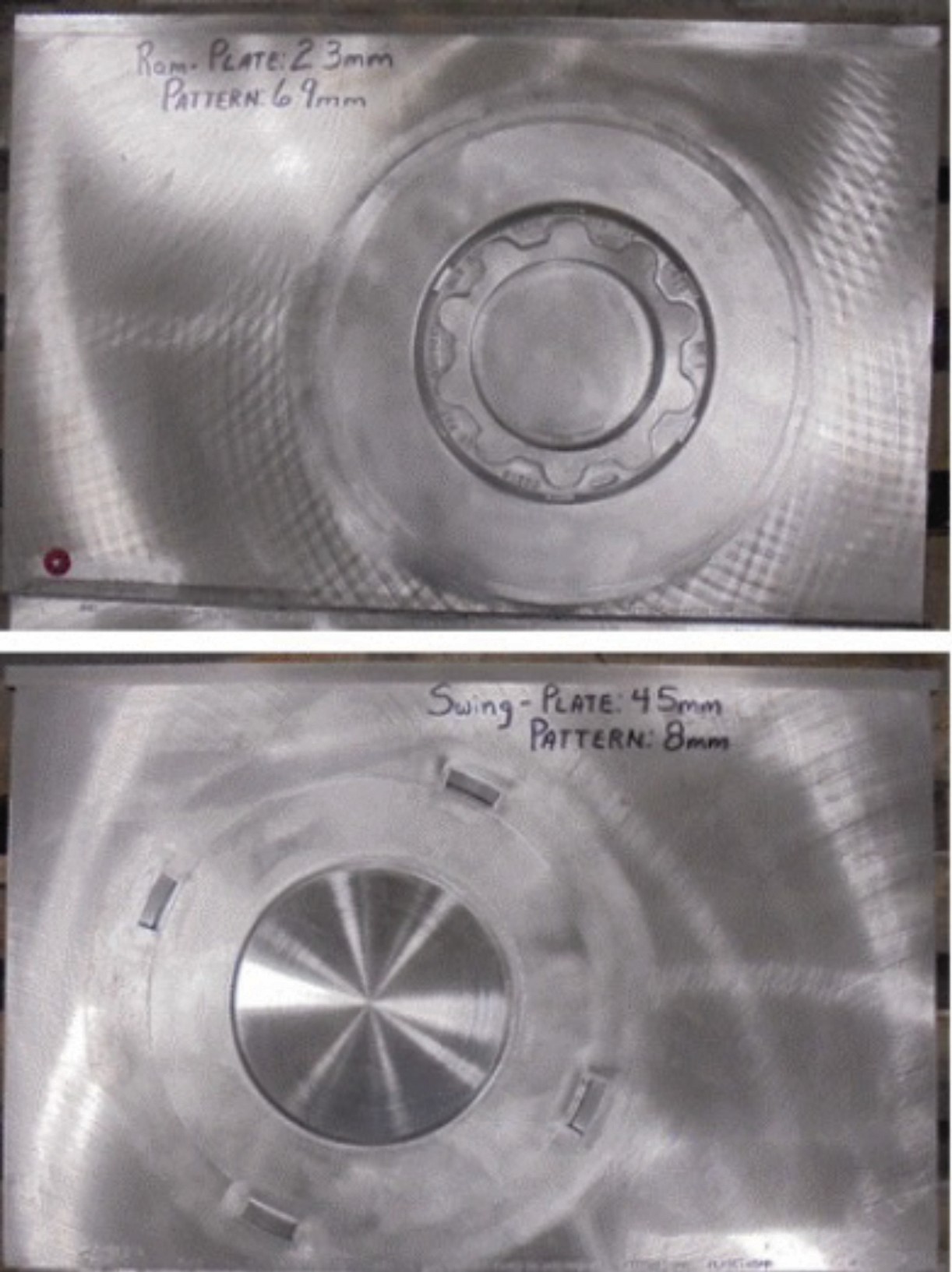
- Piece Cost: Low-Mid
- Lead Time: 4-10 weeks
- Quantity: 5-500+ pieces
3D-Printed Mold Holder
Uses Waupaca-owned 3D-printed mold holders to eliminate tooling investment while enabling production-quality iron casting pouring and processing. This method is ideal for mid-volume parts needing fast iteration. The iron casting must fit in the usable area of the printed mold holder. The printed geometry for the exterior of the casting is contained within the printed sand mold. Printed cores can be added for internal geometry.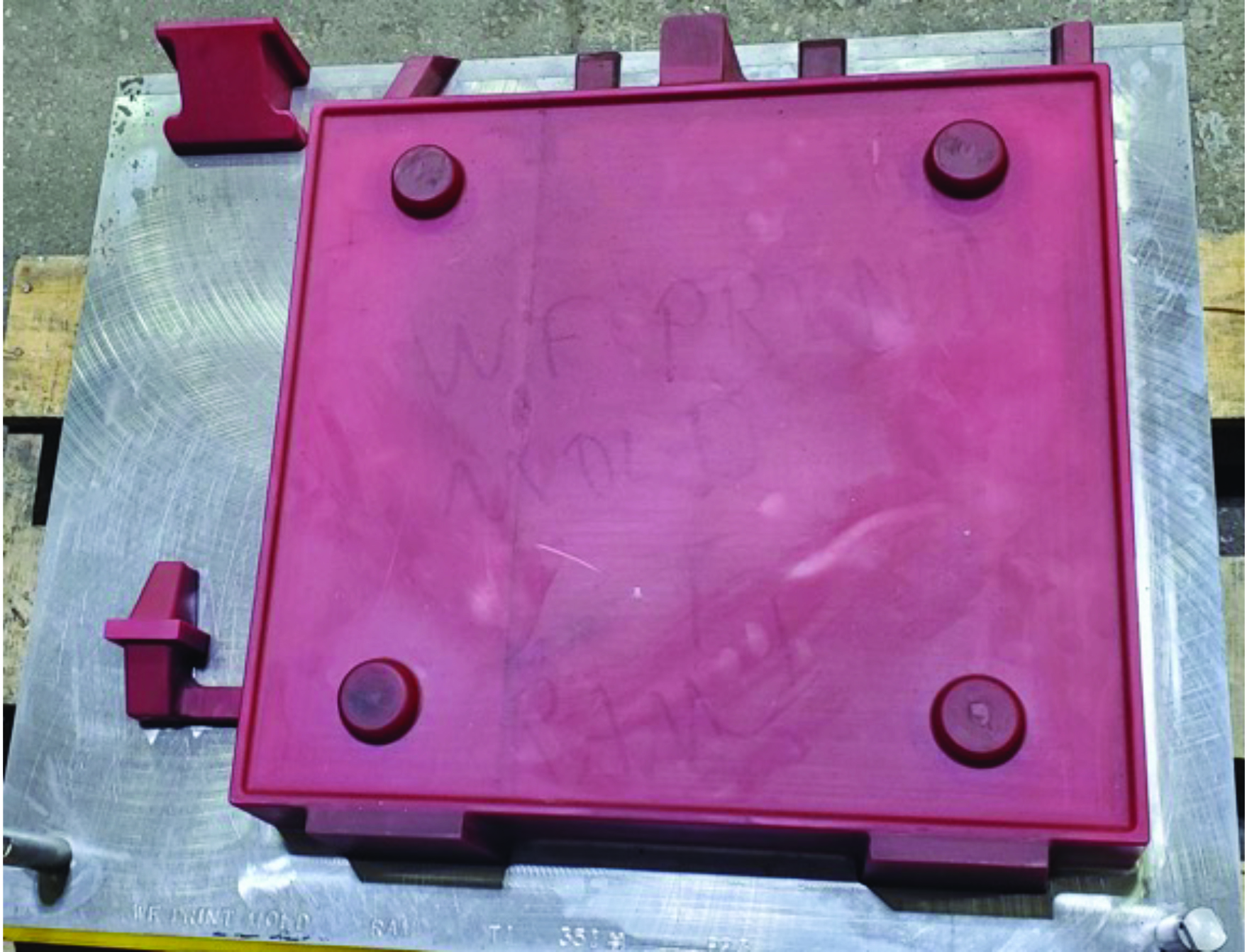
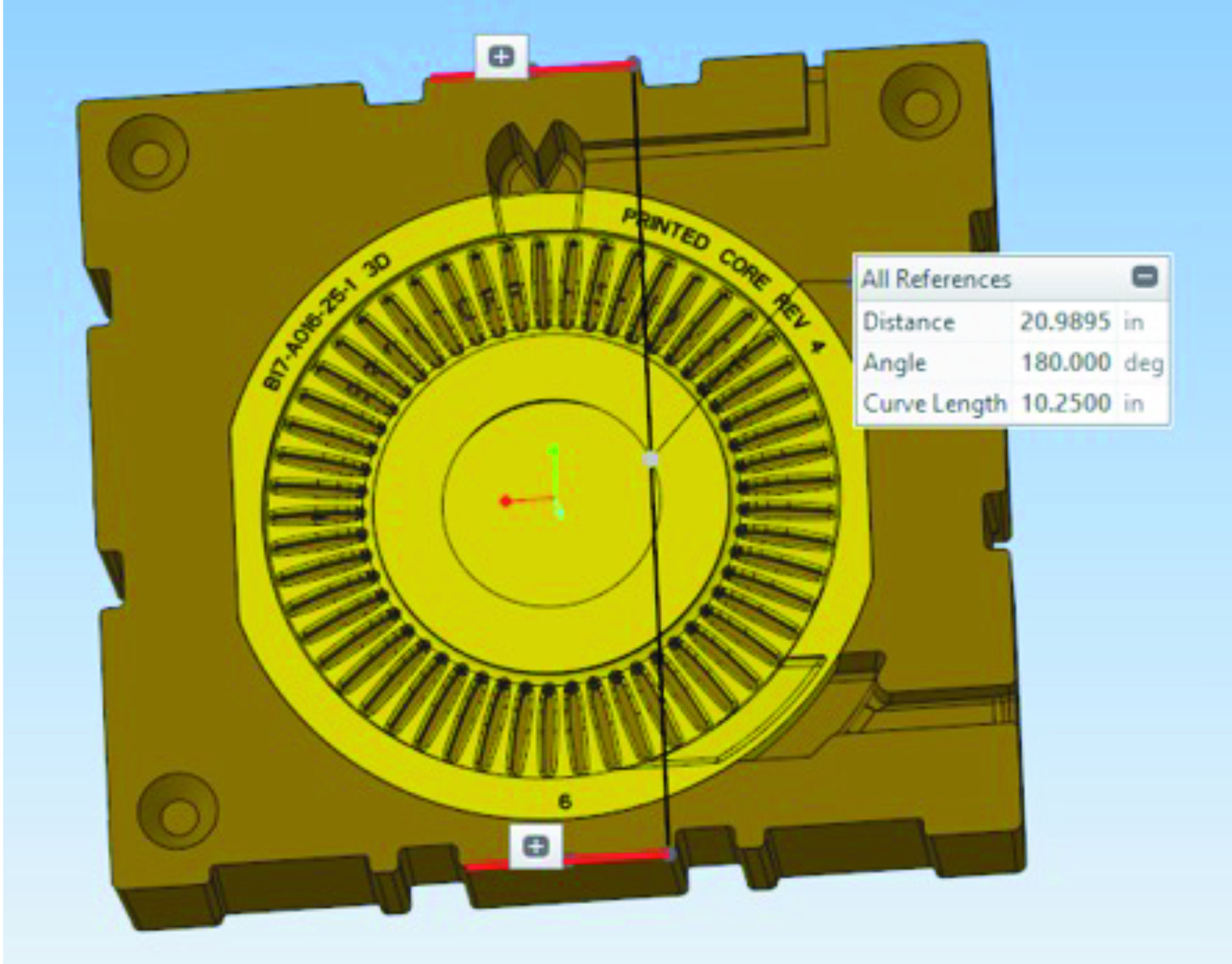
Benefits:
- Piece Cost: Mid-High
- Lead Time: 2-6 weeks
- Quantity: 5-100+ pieces
Full 3D-Printed Molds
3D-printed molds define the casting’s external shape, with optional 3D-printed cores used to create complex internal features. This offers unmatched flexibility and freedom, and no tooling is required. Casting prototypes are poured using a standard production process, but require manual handling after pouring. This method is recommended for low-volume, complex geometries or time-sensitive projects.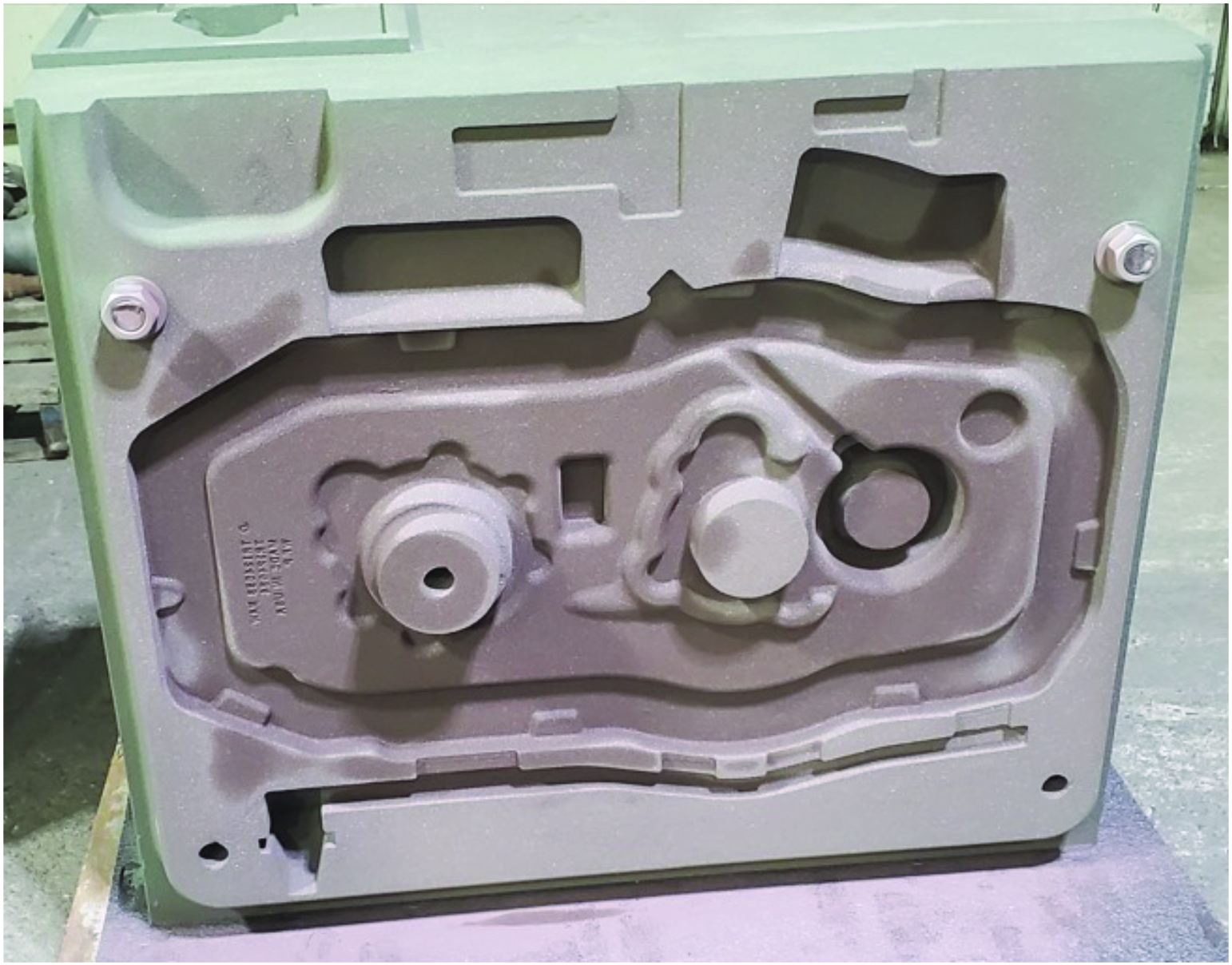
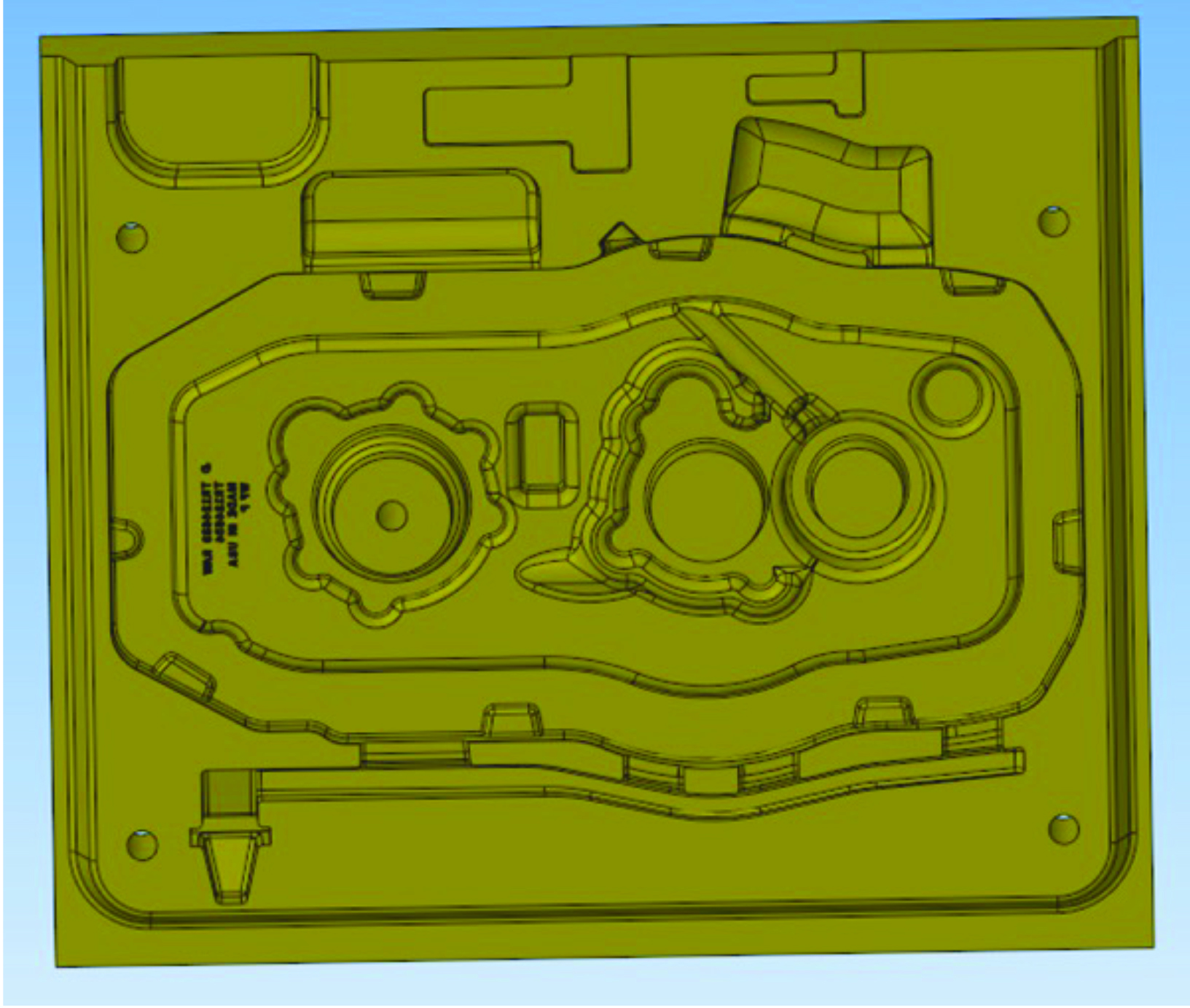
- Piece Cost: High
- Lead Time: 2-4 weeks
- Quantity: 1-15 pieces
Small-Scale 3D-Printed Molds
This method requires no tooling investment and is ideal for low-volume prototypes. Molds are limited by the volume of iron that can be hand-poured and are manually processed after casting. This method is an excellent option for early design validation before committing to other prototyping or production methods.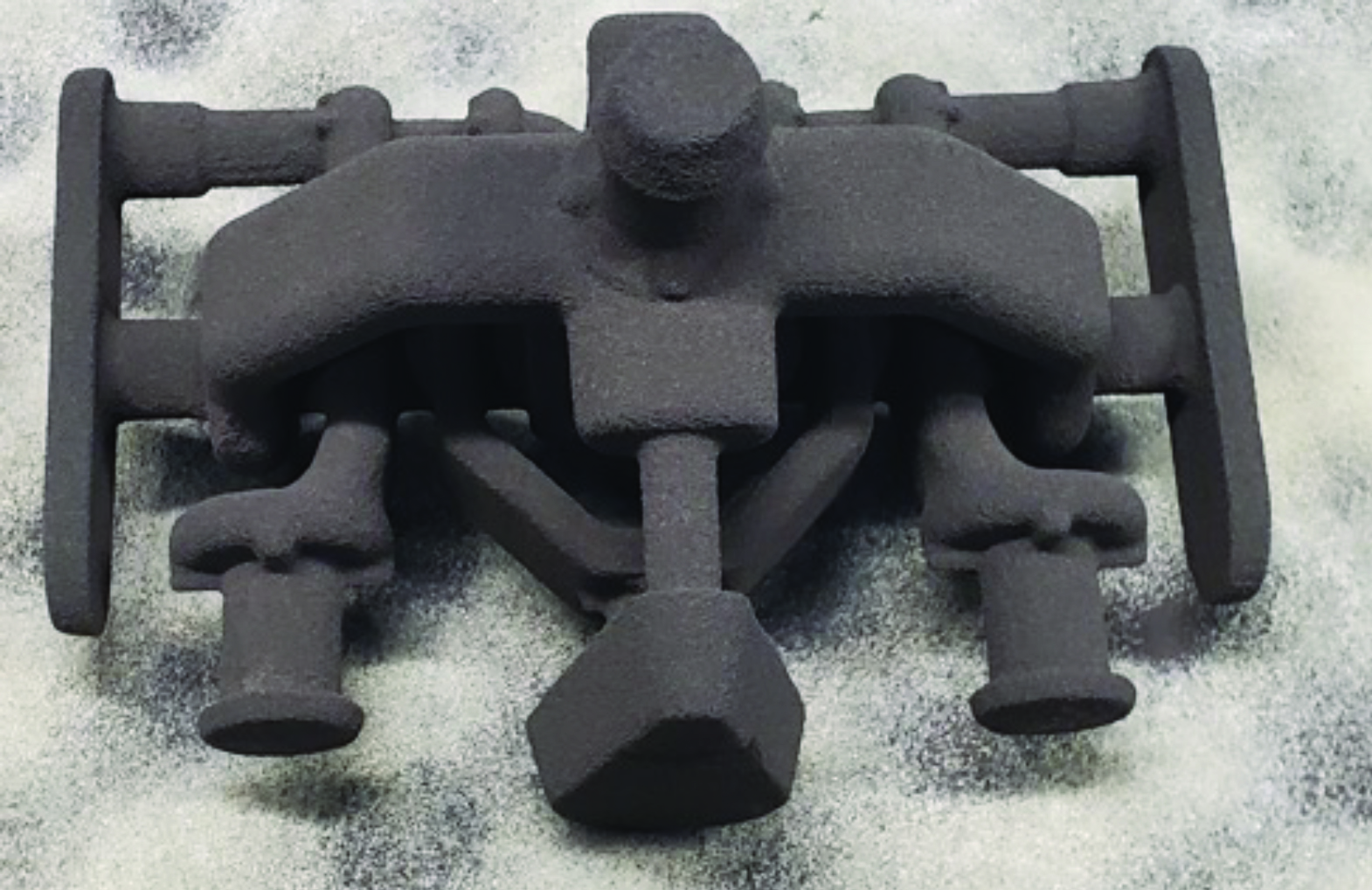
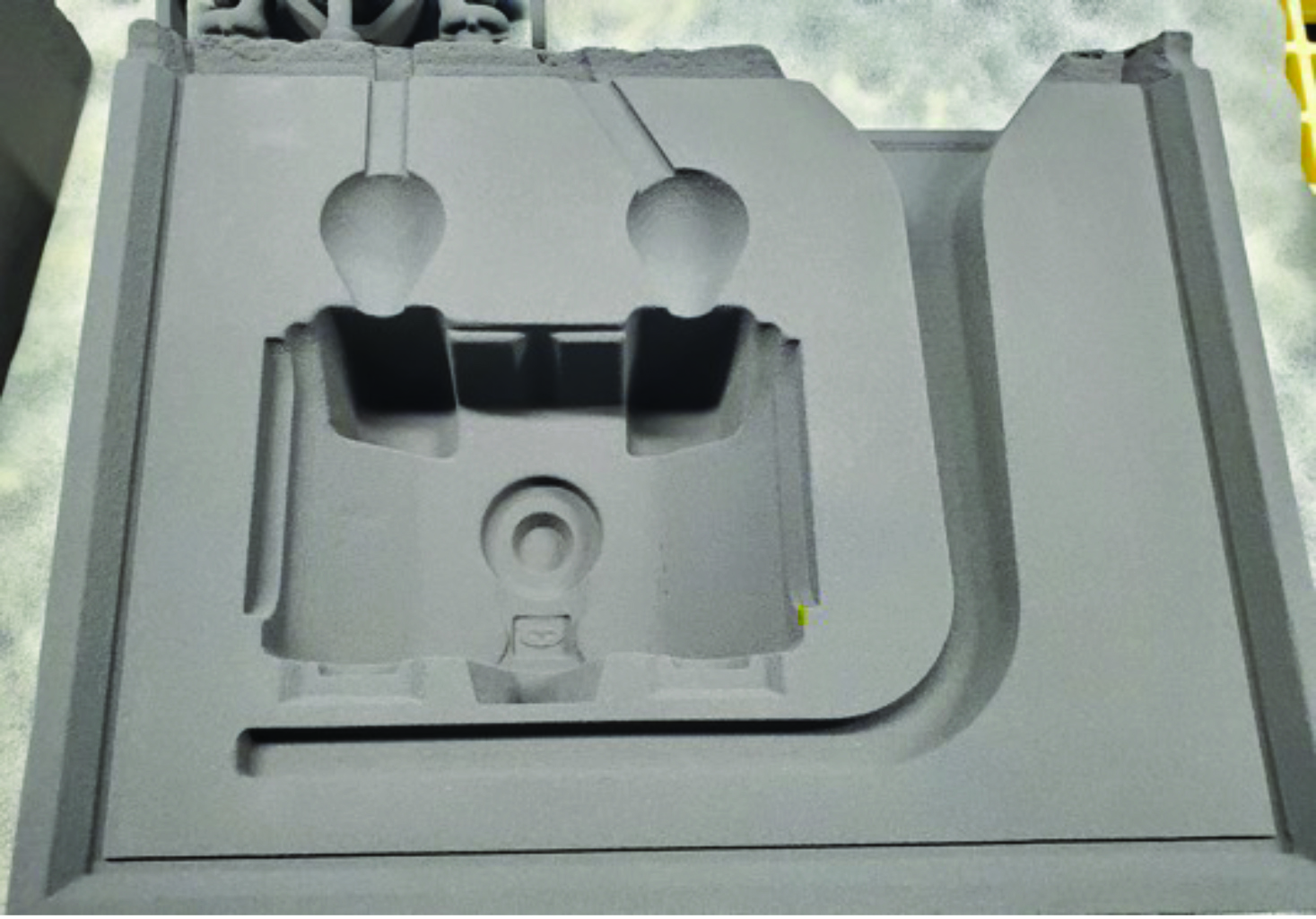
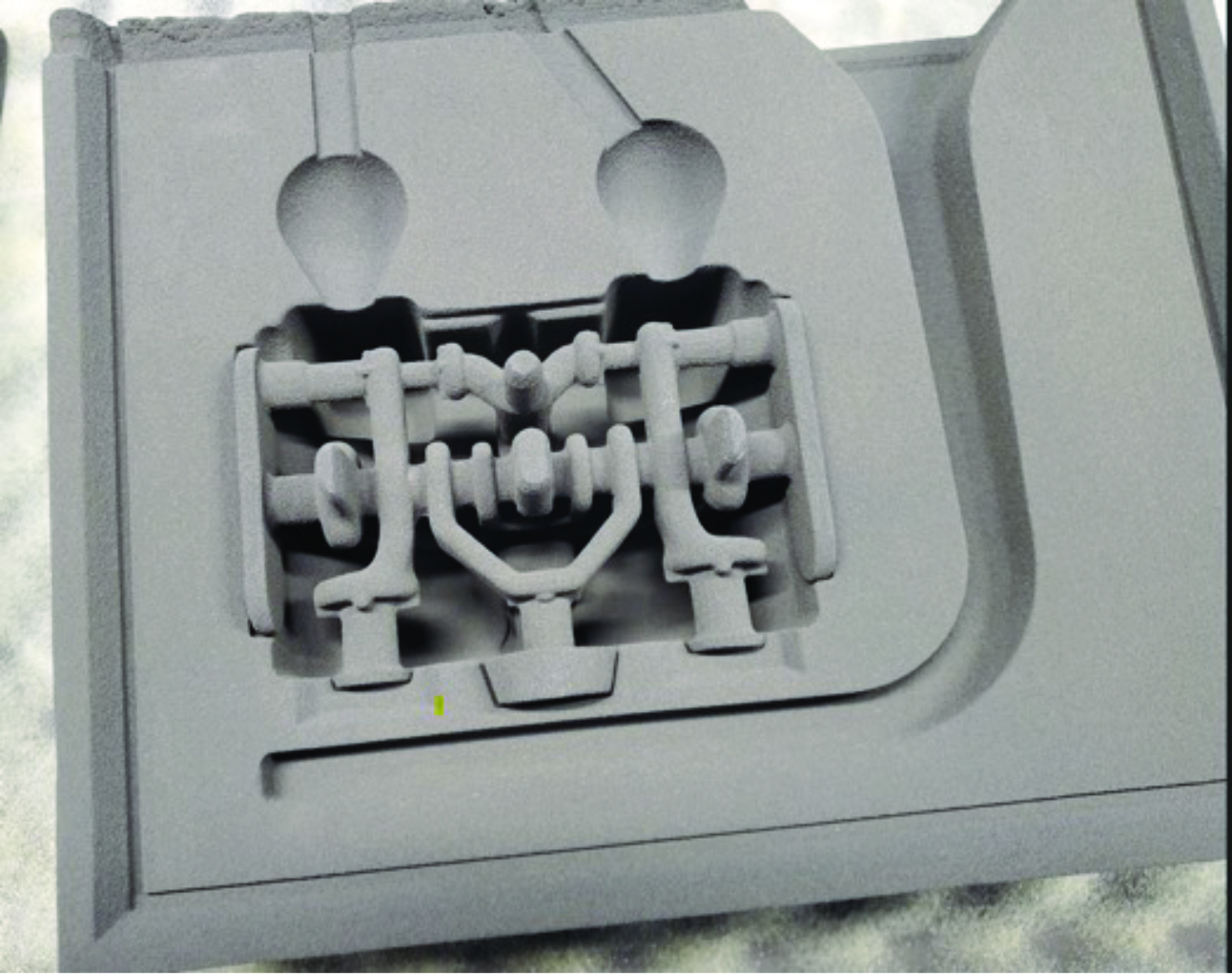
- Piece Cost: High
- Lead Time: 1-4 weeks
- Quantity: 1-10 pieces
Prototype with Confidence
From fast-turn, low-volume castings to full-scale production-quality runs, Waupaca Foundry delivers proven prototype solutions backed by world-class engineering and quality control. All under one roof.Ready to bring your casting design to life—fast?
Contact your Waupaca Foundry Key Account Manager to get started, or Contact Us to discuss the right rapid prototyping solution for your project.
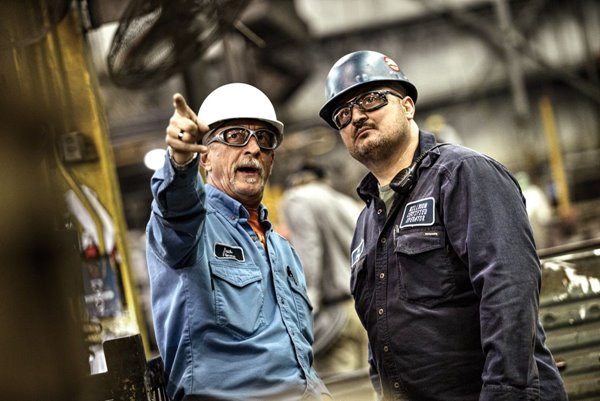