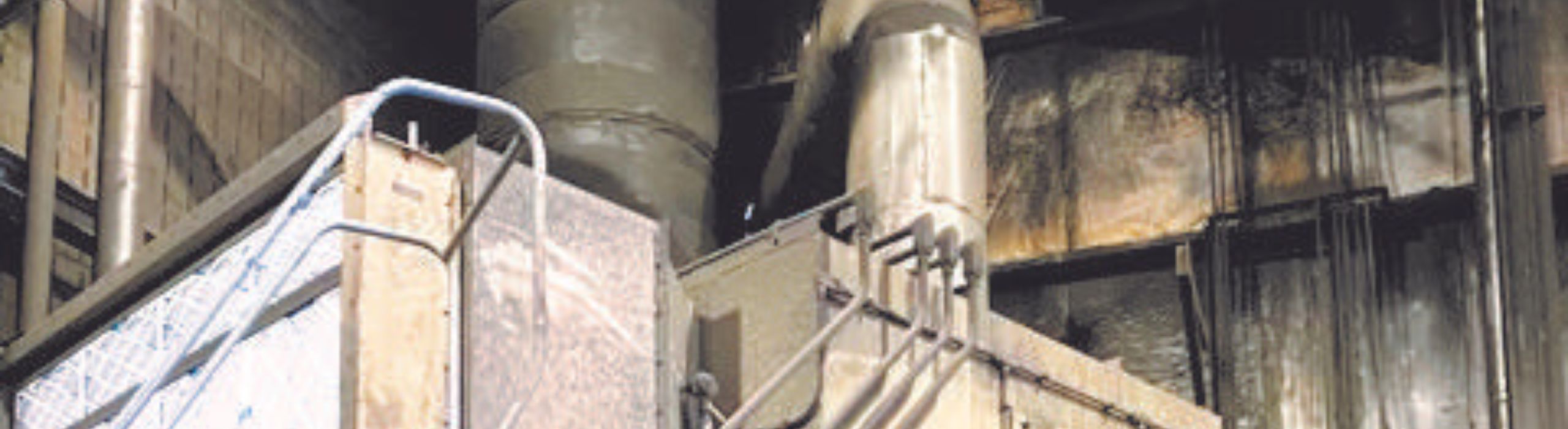
Waupaca Foundry Sustainability Commitment
The Power of Dehumidification Systems
Dehumidification system saves energy, improves efficiency.
A revolutionary blast-air dehumidification system is decreasing energy costs, decreasing raw material use, and increasing melt efficiency.
High humidity in cupola blast air has detrimental effects on cupola efficiency. When melting pig iron and scrap metals in the humid hills of the Ohio River valley, damp air works against efforts to efficiently operate a foundry cupola to the 2,800°F degrees required to melt iron. The Tell City, Indiana gray and ductile iron foundry features an annual melt capacity of 450,000 tons using cupola furnace technology. The energy used to melt iron represents 65% of the facility’s total energy use, with coke comprising the largest energy source. With relative air humidity averaging 80% (with many days at 100% humidity), there was a potential improvement opportunity.
Humid intake air was affecting the efficiency of the cupola causing increased coke use per unit of iron melted, lower combustion temperatures, reduced carbon pickup and elevated thermal oil heat loads increasing exhaust volume to the emission system. When melting iron, the 75-foot-tall cupola consists of alternate layers of scrap metal, coke as an additive and fuel, and limestone flux. The coke is consumed in ambient air which is introduced by the blast air blowers and oxygen injection system.
The hot gases generated in the lower part of the shaft ascend and preheat the descending charge. In response the plant installed a blast-air dehumidification system to compensate for high humidity conditions. The system uses a 7-foot desiccant drying system to remove water vapor from ambient air prior to blast preheating in the recuperative heat exchanger. The heat exchanger is regenerated using reclaimed waste heat from the thermal oil cooling system, thus minimizing operating costs and providing the most positive energy balance and environmental benefit. The system reduced blast humidity to levels as low as 7 to 10 grains of water per pound of dry air.
The resulting annual reduction in coke consumption and cupola efficiency gains are significant — at 1.19 lbs. of coke reduction for every pound of moisture removed, this allowed a reduction of 2.5% of total coke usage and represented a savings of $335,000 per year.
- Improved cupola melting efficiency by 3%.
- Reduced coke use by 656 tons annually.
- Avoided 1,804 CO2-tons of GHG emissions.
- Reduced total plant energy use by 1%.