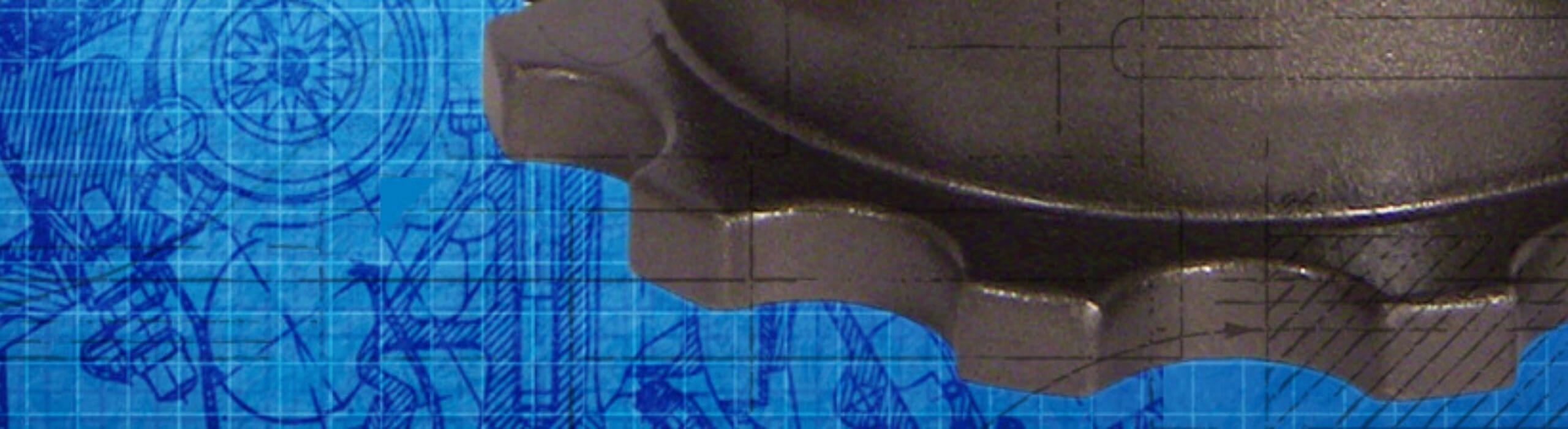
Case Study
Waupaca Foundry Steering Column Collaboration
Waupaca Foundry leveraged 3D printing to provide an improved iron casting design 2-3 weeks ahead of the customer’s lead time. This solution offered the customer flexibility to test the design faster, mitigated risk, and provided a cost savings. When combined with Waupaca Foundry’s responsiveness and desire to collaborate on best-in-class solutions, the 3D printing capabilities delivered tangible benefits.
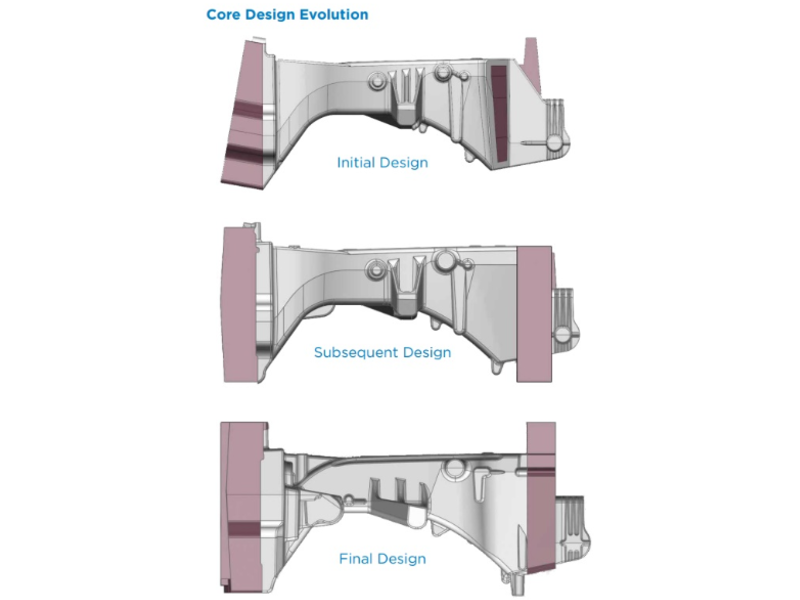
Engineers at a global agricultural equipment OEM initiated a redesign of a tractor steering column support and needed immediate turnaround. The interior of the 111-pound gray iron casting was formed by a series of three cores with features that were required to improve critical airflow. In addition to the time constraints, there remained questions concerning the exact geometry of the part’s interior.
Waupaca Foundry recommended that the cores for the gray iron casting be 3D printed to reduce the timeline and avoid the risk of uncertain geometry. The OEM could also avoid the cost of core box tooling.
Another advantage Waupaca Foundry presented by using 3D printed cores was the ability to make multiple iterations of the part. This allowed the customer the option to request a run of several designs in tandem, again without the hard tooling costs.

From the time of purchase order, the 3D-printed cores were completed and delivered in eight days—an exceptional turnaround considering the complexity, size and weight of the 79-pound core assembly. As a result of using 3D printed cores and the responsiveness of Waupaca Foundry, the OEM saved 2-3 weeks on the project lead-time and was able to test their rapidly prototyped iron castings quicker.
The OEM also realized a 20% costs savings on the project.
- Delivered 3D printed cores in only 8 days.
- Saved 2-3 weeks on the project lead-time.
- Saved the OEM on hard-tooling costs; overall, saved 20%.
- Allowed for multiple iterations of geometry to be produced and tested without the risk of high cost modifications or the potential of the coremaking equipment becoming obsolete