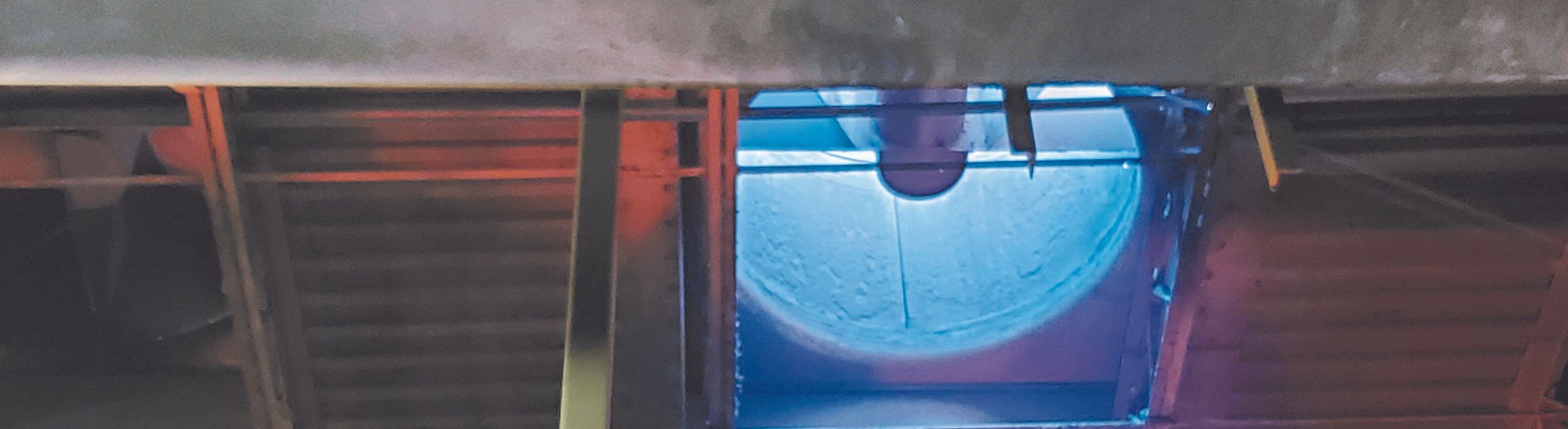.jpg)
Waupaca Foundry Sustainability Commitment
Energy-Efficient Airflow Solution
Smart Ventilation System Saves Energy
Automation, technology, and innovation are at the heart of one of the world’s oldest industries. At Waupaca Foundry located in Waupaca, Wisconsin, the linked foundries Plant 2 and Plant 3 share a melt center and cycle more than 1 million cubic feet of air every minute. Air is constantly monitored for quality, worker comfort, and consistent temperature across the 665,850 square foot gray iron foundries.
Within the facility’s sand mulling and molding departments, six roof-mounted exhaust fans remove heat and circulate air during the summer months. Prior to the system upgrade, exhaust fans ran continuously and did not adequately address seasonal temperature variations. In the cooler winter months, this resulted in the work area being too cold and/or nearby make-up air fans unnecessarily replacing the air volume and building comfort heat. The exhaust system became a focus of internal continual improvement teams.
“We had been focusing on energy management for many years, but automation is a really big initiative in manufacturing. In this case, it was an answer to saving energy,” said Tim Wideman, Assistant Maintenance Manager for Waupaca Foundry.
In-house engineers designed a new system using off the shelf technology. Existing fans were automated with temperature and carbon monoxide sensors to became a “smart” system; triggering fan operation only when workplace temperatures were elevated and/or carbon monoxide levels required dissipation.
An improvement in workplace ventilation balance and comfort was realized. The addition of a carbon monoxide automation control increased workplace safety, ensuring that carbon monoxide levels were actively monitored and subject to appropriate ventilation control.
The redesigned exhaust system resulted in significant energy savings with no loss in system performance. Compared to the prior continual operation, the added smart controls reduced 275,000 kWh of electricity and 28,000 dkt of natural gas, annually representing approximately $124,000 in energy savings annually.
As a result, the Wisconsin Manufacturers and Commerce (WMC) recognized Waupaca Foundry’s smart exhaust system project with the Business Friend of the Environment award in the large business category in 2022.
Melting iron is energy intensive and any improvement in the process, no matter how small, can yield big results. Installing “smart controls” on exhaust fans yielded results:
- Reduced energy use by 275,000 kWh annually — the equivalent energy to power 26 residential homes.
- Reduced energy use by 28,000 dkt of natural gas annually.
- Improved workplace ventilation and increased worker comfort.
- Ensured carbon monoxide levels were actively monitored.