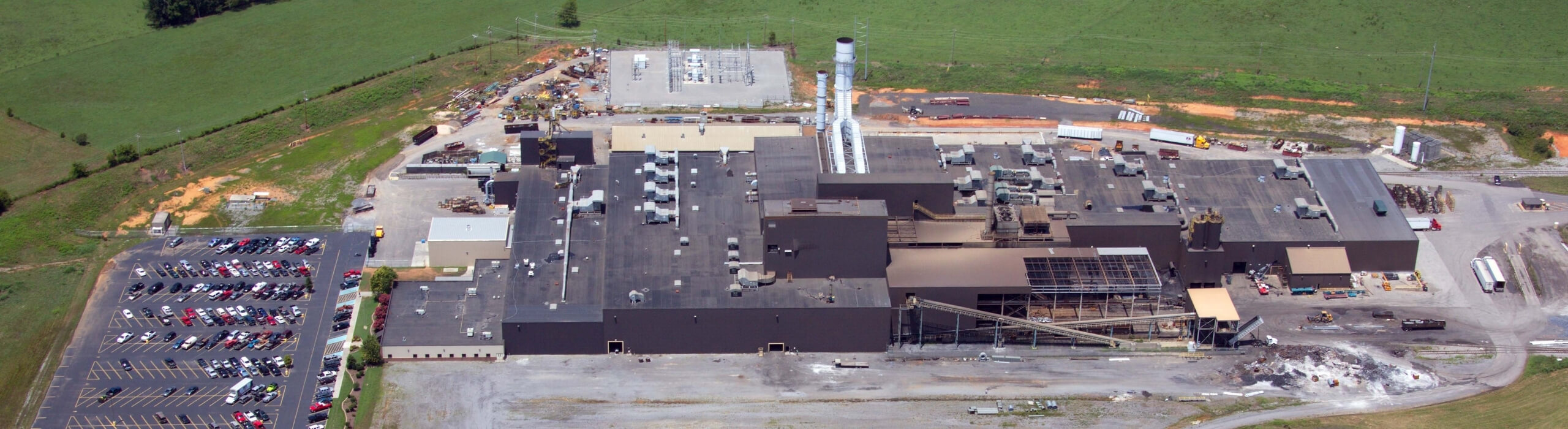
Waupaca Earns Energy Incentives
LED Lighting Upgrades Enhance Safety, Save Energy
Aug. 14, 2015—Waupaca Foundry Inc., announces it received a $399,830 incentive from Etowah Utilities for an energy conservation program managed by Tennessee Valley Authority (TVA) called EnergyRight® Solutions for Business. In June 2015, the Waupaca Foundry plant in Etowah, Tennessee replaced 75% of lighting fixtures in office and plant locations with energy-saving LED fixtures making it the largest lighting upgrade for the foundry. The Etowah plant is located at 134 Waupaca Drive and employs 560 workers.
Acording to Michael Hoecker, energy manager for Waupaca Foundry, the upgrade was made to save energy and improve worker safety. "The biggest improvement comes from higher quality lighting and more uniform light levels on the plant floor," Hoecker said. "Increased light levels and lower shadows reduce worker eye strain and improve the quality inspection process, while enhancing safety for the entire work force. It also provides increased visibility for our fork truck drivers." Roy Johnson, Etowah electrical technician, adds that maintenance savings will be improved over time due to the much longer lifespan of LED lights.
Waupaca Foundry leaders estimate the lighting upgrade will save approximately 60% of lighting costs at the Etowah plant over a typical year. Replacing conventional lights with LED lights will save the gray and ductile iron foundry about 5,088,000 kilowatt hours which is equivalent to the annual electricity use of 339 average Tennessee homes. From an overall environmental perspective, Hoecker says this amount is a reduction of 2,933 tons per year of CO2 emissions which equates to 885 acres of trees planted per year.
For employees, the lighting contributes to pride in their workplace and in their product. "The brighter lighting easily allows us to spot problem areas that may have been overlooked previously," said Troy Moses, shift molding foreman.
The upgrade is part of Waupaca Foundry's corporate goal to reduce energy costs and achieve sustainable growth by the year 2020. Those goals include:
- Reducing energy use by 25%,
- Promote state-of-the-art pollution control technologies,
- Reduce spent foundry sand by 30% to reuse/recycle sand used in the metalcasting process,
- Reduce water use by 80%.
According to Waupaca Foundry CEO Gary Gigante, sustainability is central to ductile iron and gray iron casting operations. "Being environmentally responsible is not only the right thing to do, it's the best thing to do for our employees and our customers," Gigante said. "Pollution control and recycling ensures a healthy environment for our team members and creating a sustainable manufacturing process controls cost for our customers," he said.
Tennessee Valley Authority offers custom incentives through the EnergyRight® Solutions for Business program designed to help businesses overcome financial or internal barriers to installing energy-efficient equipment upgrades. "We are excited to partner with Waupaca Foundry to help them lower their energy costs, reduce their carbon footprint and better compete in the global marketplace," said Cindy Herron, Vice President of EnergyRight and Renewable Solutions. "EnergyRight Solutions is an important TVA and Etowah Utilities program that allows businesses to save money and become better environmental stewards, while continuing to thrive and keep jobs in the Valley.
"Etowah Utilities is very happy that Waupaca Foundry has been able to take advantage of the incentives offered through the EnergyRight® Solutions for Business program. The iron casting plant is an important member of the Etowah community and we are glad to be able to improve their operations through this project," said Ronnie Camp, electric superintendent.
Waupaca Foundry has a similar lighting upgrade in progress at its Marinette, Wis. foundry, which is scheduled for completion in September 2015. One of three plants located in Waupaca, Wis. received energy reimbursements earlier this year from Wisconsin's Focus on Energy for a heat recovery system. The foundry is currently investigating lighting upgrades at all other facilities, but has already completed a wide variety of other sustainability projects over the past few years, including:
- Waste heat recovery from each cupola melt furnaces at all three Waupaca, Wis. foundries. These heat recovery systems supply the majority of the winter space heating and hot water requirements without using additional fuel.
- Approximately 70 percent of foundry sand byproducts that can no longer be used in metalcasting is cleaned and reused in local projects including road and general construction, agriculture and geotechnical fill. The firm has been recycling foundry sand and related materials for more than two decades.
- Closed-loop cooling water systems have reduced plant water cooling demands by 80 percent or more when all are on-line. In some cases, non-contact cooling water discharges are reduced to near zero and daily water use is drastically reduced.
- The company began retrofitting plants with sophisticated air pollution controls beginning in 1999. Both air emission controls and leak detection technology have surpassed regulatory requirements and created new industry benchmarks in pollution control.
For more information on sustainability efforts underway throughout Waupaca Foundry, please visit the website at www.waupacafoundry.com/en/our-company/citizenship/sustainability.
###